Surface treatments play a critical role in the precision metal industry. They enhance not only the visual appeal but also the functionality, durability, and resistance of metal products. Here, we’ll explore 12 essential surface treatments, each with unique benefits, applications, and processes that make them invaluable in precision engineering, manufacturing, and end-use environments. Whether you’re looking to protect metal parts against corrosion, enhance wear resistance, or create a specific aesthetic, this guide will provide you with the insights needed to choose the right surface treatment for your needs.
1. Anodizing
What It Is: Anodizing is an electrochemical process that thickens the oxide layer on metals, primarily aluminum, to improve corrosion resistance and allow for color dyeing.
Process: The metal is submerged in an acid electrolyte bath, where an electric current flows through, causing oxidation on the surface. This process forms a porous layer that can then be dyed or sealed.
Benefits:
- Increased corrosion resistance
- Enhanced durability and hardness
- Aesthetic versatility with color options
Applications: Widely used in aerospace, electronics, and consumer goods for both aesthetic appeal and functional longevity.
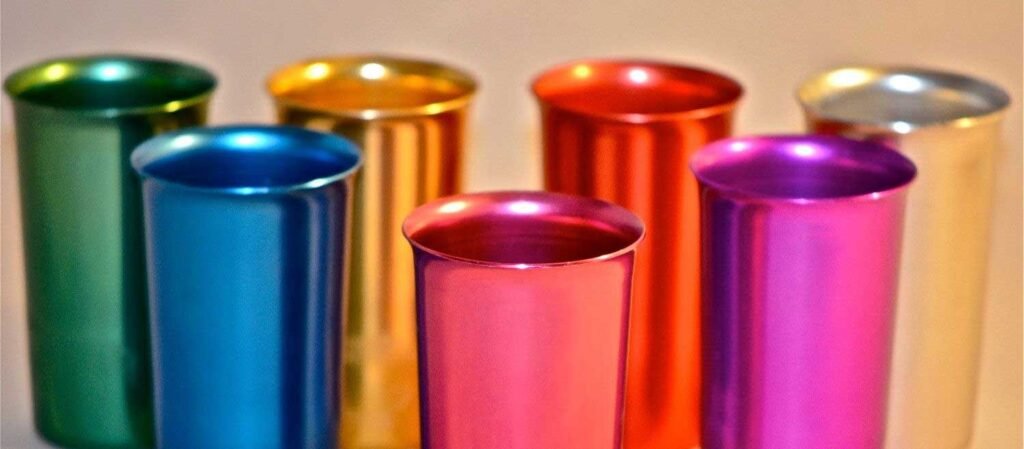
2. Electroplating
What It Is: Electroplating involves coating a metal surface with a thin layer of another metal, such as nickel, chrome, or gold, through an electrochemical process.
Process: The object to be plated is submerged in an electrolyte solution, and a current is applied, causing metal ions to bond to the surface.
Benefits:
- Improved corrosion resistance
- Increased hardness and durability
- Enhanced appearance with various finishes
Applications: Common in automotive, jewelry, and electronics for aesthetic and protective purposes.
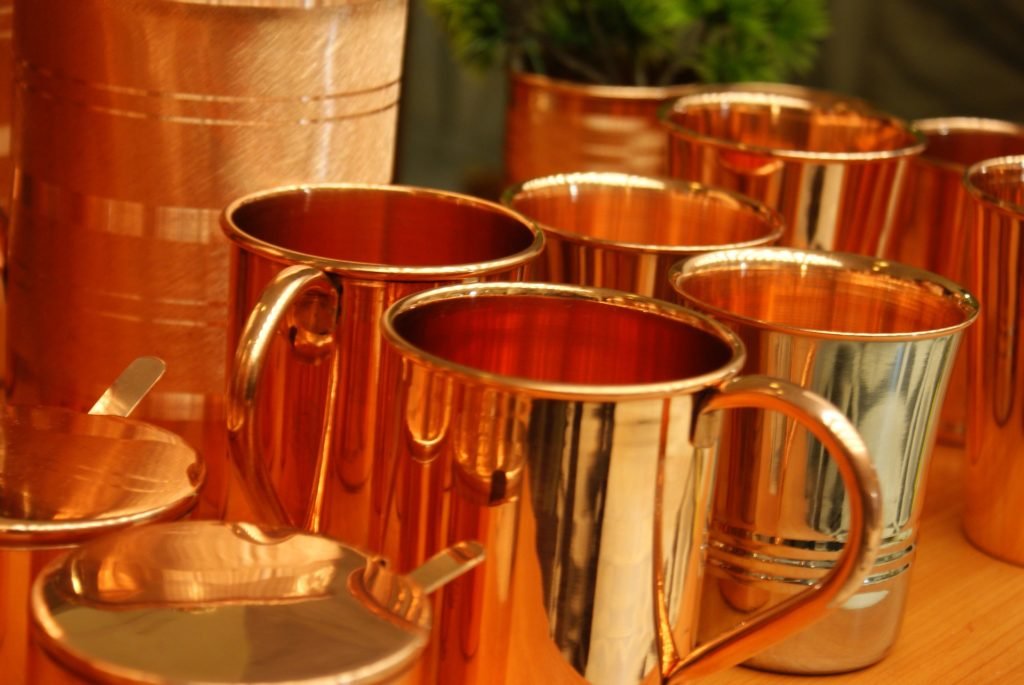
3. Passivation
What It Is: Passivation is a chemical process that removes free iron from the surface of stainless steel, allowing for the formation of a thin, protective oxide layer.
Process: The metal is cleaned and then treated in an acid bath, often nitric or citric acid, which removes contaminants and promotes oxide layer formation.
Benefits:
- Enhanced corrosion resistance
- Cleaner, contaminant-free surface
Applications: Essential in medical, food processing, and aerospace industries where stainless steel is frequently exposed to corrosive environments.
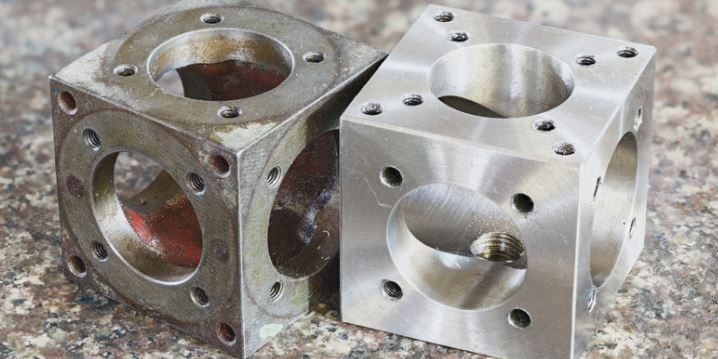
4. Powder Coating
What It Is: Powder coating is a dry finishing process where a powdered paint is electrostatically applied to metal surfaces and then cured under heat to create a durable, uniform finish.
Process: The metal is cleaned, the powder is applied electrostatically, and then it’s baked in an oven to cure, forming a tough, protective layer.
Benefits:
- Excellent wear resistance and durability
- Available in a wide range of colors and textures
- Environmentally friendly as it contains no VOCs
Applications: Used in automotive, appliances, and outdoor metal products for decorative and protective purposes.
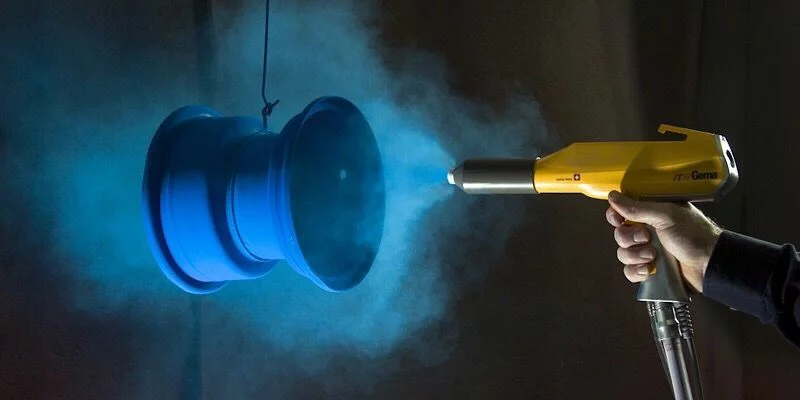
5. Phosphating
What It Is: Phosphating, or phosphatizing, creates a layer of phosphate coating on metal surfaces, enhancing corrosion resistance and providing a base for paint adhesion.
Process: Metal parts are immersed in a phosphoric acid solution, where a chemical reaction forms a crystalline phosphate layer on the surface.
Benefits:
- Improved paint adhesion
- Enhanced corrosion resistance
- Cost-effective process for large production runs
Applications: Popular in the automotive and military industries as a primer for further coating.
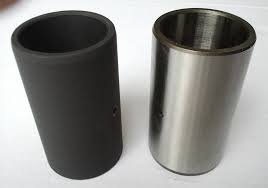
6. Black Oxide
What It Is: Black oxide is a conversion coating applied to ferrous materials to create a sleek black finish that reduces light reflection and enhances corrosion resistance.
Process: Metal is dipped in a solution of alkaline salts, creating a black oxide layer on the surface. Post-treatment oil can be applied for additional corrosion protection.
Benefits:
- Low-cost and durable finish
- Improved corrosion resistance when oiled
- Aesthetic appeal with matte black appearance
Applications: Common in tool manufacturing, firearms, and optical instruments.
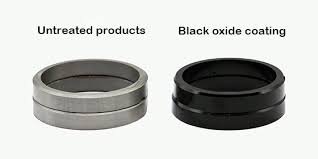
7. PVD (Physical Vapor Deposition)
What It Is: PVD coating is a high-tech process that deposits thin, hard coatings onto metal surfaces, enhancing wear resistance and providing aesthetic finishes.
Process: A thin film of coating material (e.g., titanium nitride) is vaporized in a vacuum chamber and then condenses onto the metal surface, creating a hard, durable layer.
Benefits:
- High hardness and wear resistance
- Excellent aesthetic properties with color options
- Environmentally friendly process
Applications: Used in high-end tools, decorative items, and cutting instruments.
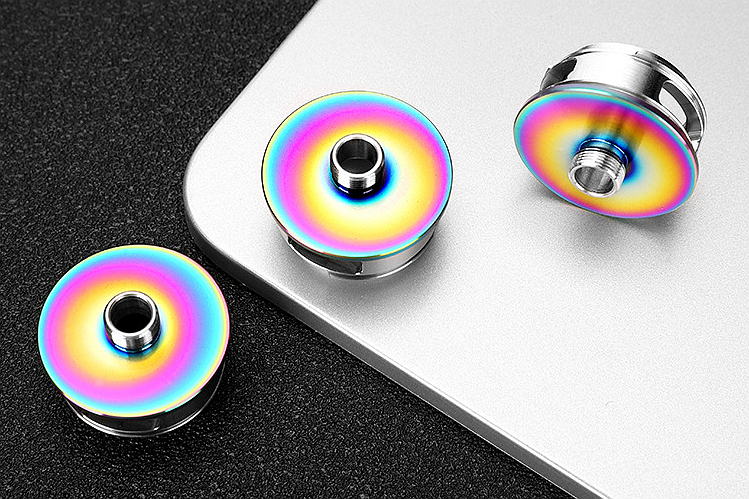
8. Hot-Dip Galvanizing
What It Is: Hot-dip galvanizing involves dipping steel into molten zinc, creating a thick, corrosion-resistant coating that’s ideal for outdoor applications.
Process: Cleaned steel is immersed in a bath of molten zinc, forming a metallurgical bond that provides long-lasting protection against rust.
Benefits:
- Excellent corrosion resistance
- Low maintenance and long-lasting
- Economical for large structures
Applications: Common in construction, agriculture, and marine environments where metal parts are exposed to the elements.
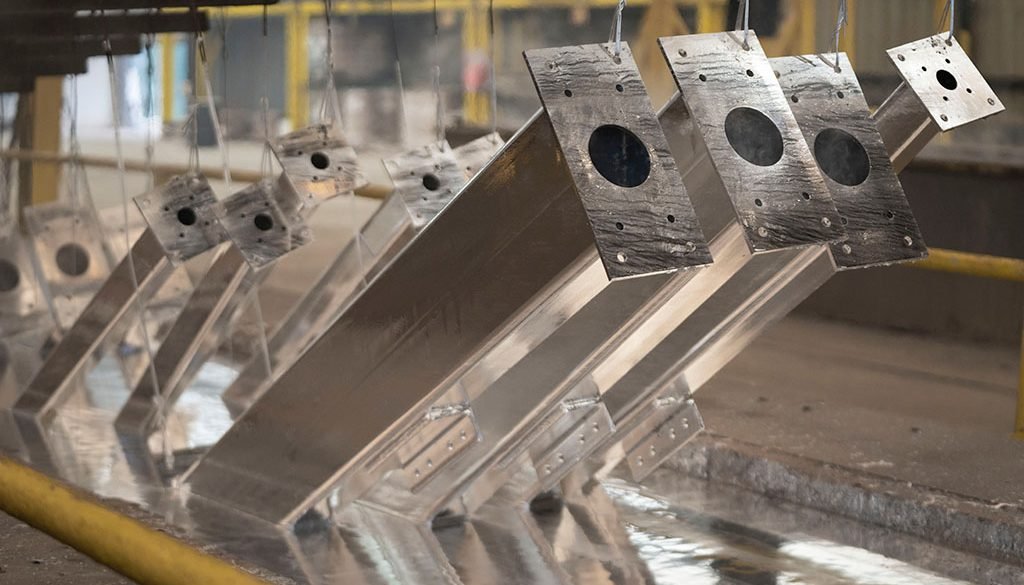
9. Chemical Conversion Coating
What It Is: Chemical conversion coating involves applying a thin, protective layer on metals, commonly through chromating or phosphating, to improve corrosion resistance and paint adhesion.
Process: Metal is treated in a solution that reacts with the surface, forming a protective layer without adding thickness.
Benefits:
- Improved paint adhesion and corrosion protection
- Minimal dimensional change
- Cost-effective for large batches
Applications: Often used in automotive and aerospace industries, especially for aluminum and steel.
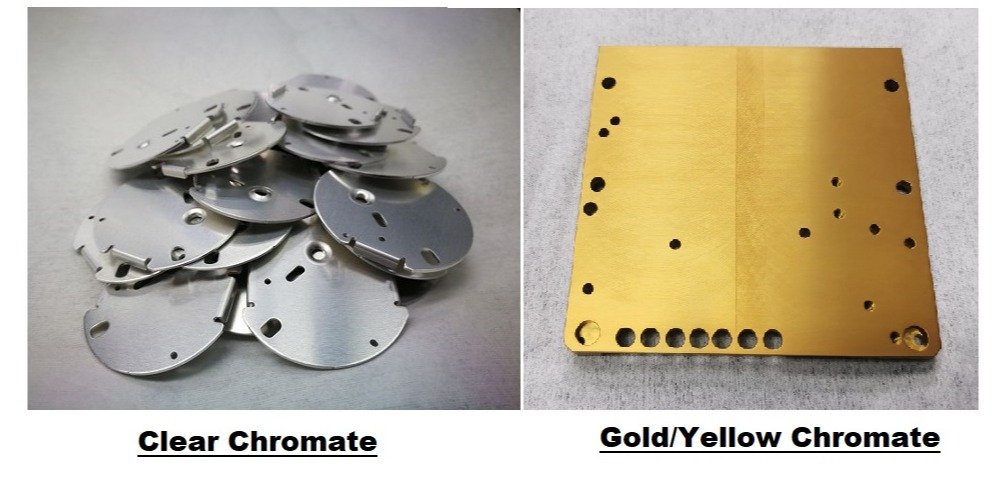
10. Laser Surface Treatment
What It Is: Laser surface treatment involves using high-intensity laser beams to modify or harden metal surfaces, increasing wear resistance and extending product life.
Process: A laser beam is directed at the metal surface, heating and altering its microstructure, resulting in localized hardening or surface texture changes.
Benefits:
- Precise control over treated areas
- Improved surface hardness and wear resistance
- Can be tailored for complex geometries
Applications: Often used in cutting tools, molds, and components that require high surface hardness.
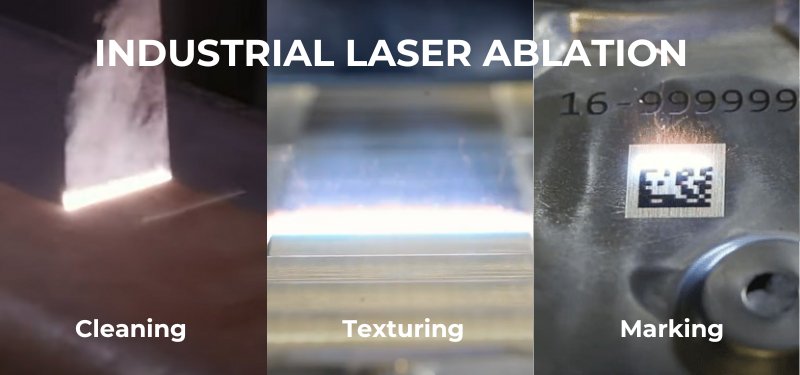
11. Electropolishing
What It Is: Electropolishing is an electrochemical process that smooths and polishes metal surfaces by selectively removing material, leaving a bright and smooth finish.
Process: Metal parts are submerged in an electrolyte solution and subjected to an electrical current, dissolving microscopic peaks on the surface.
Benefits:
- Superior smoothness and brightness
- Increased corrosion resistance
- Reduction in microbial contamination
Applications: Common in medical, food processing, and pharmaceutical industries for stainless steel components.
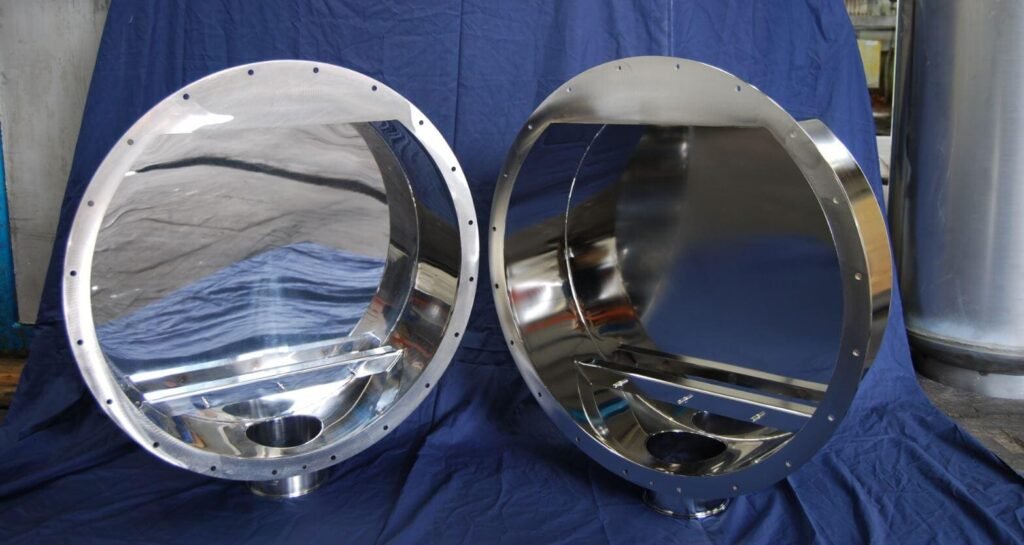
12. Sandblasting
What It Is: Sandblasting uses abrasive particles propelled at high speed to clean, roughen, or smooth a metal surface, preparing it for further treatment.
Process: Abrasive material (sand, glass beads, or aluminum oxide) is blasted onto the metal surface, removing contaminants and creating a rough texture.
Benefits:
- Effective for cleaning and surface preparation
- Removes rust, paint, and oxidation
- Creates an ideal base for coatings and paint
Applications: Used across many industries, especially for cleaning and prepping surfaces before painting or coating.
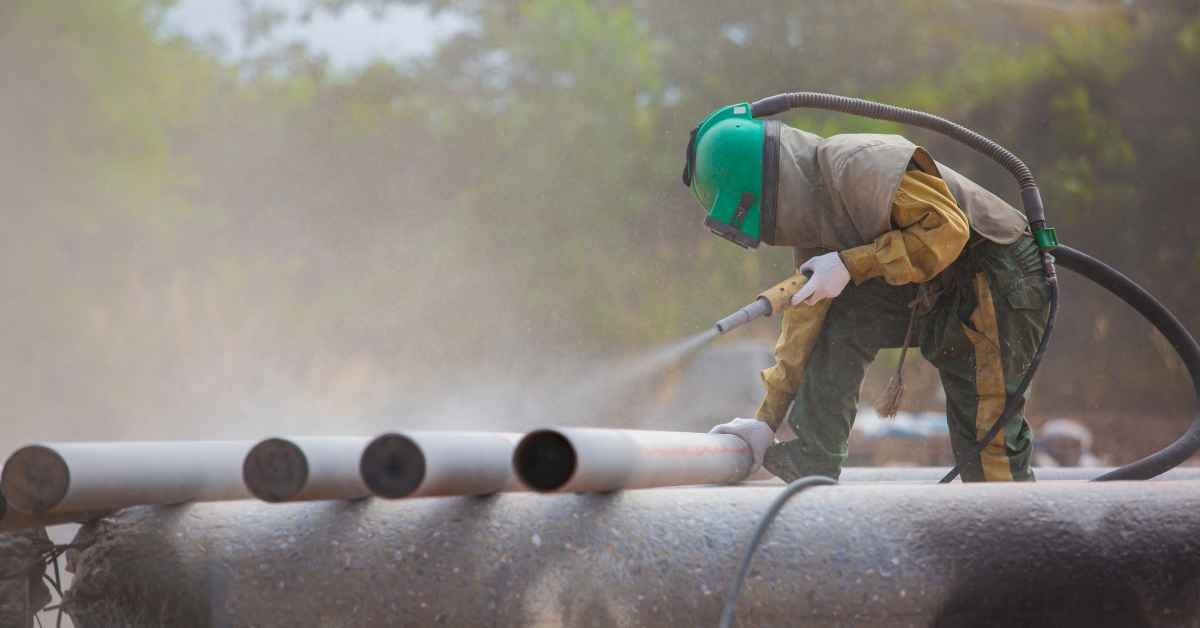
Choosing the Right Surface Treatment for Your Needs
Selecting the ideal surface treatment depends on the specific application, type of metal, desired aesthetic, and required durability. Each treatment has unique advantages and drawbacks. For example:
- Corrosion resistance is paramount for parts in marine or harsh environments, making hot-dip galvanizing or anodizing ideal.
- Wear resistance is critical for tools and parts subject to abrasion, for which PVD and laser treatments offer durable solutions.
- Aesthetic appeal and texture requirements vary, with options like powder coating, anodizing, and electropolishing providing a range of finishes and colors.
Conclusion
Surface treatments for precision metals are as varied as they are essential, each tailored to enhance the performance and aesthetics of metal products. By understanding the benefits and applications of these 12 core treatments, industry professionals can make informed choices that enhance the longevity, appearance, and functionality of their metal components, ultimately contributing to high-quality, durable, and aesthetically appealing products.
At LUX Metal, we understand the importance of precision and excellence in metal fabrication. Our expert team and state-of-the-art facilities allow us to tackle even the most challenging projects with confidence. To learn more about our metal fabrication services, visit our website at LUX Metal.
References
For further reading, explore these resources to learn more about the benefits and applications of cold-formed steel in modern construction: