1. The Rise of Asia as a Manufacturing Powerhouse
Asia has long been a global manufacturing leader. China’s rapid industrialization in the late 20th century cemented its position as the “world’s factory.” At the same time, Southeast Asian countries like Vietnam, Thailand, Malaysia, and Indonesia have also established themselves as competitive manufacturing destinations.
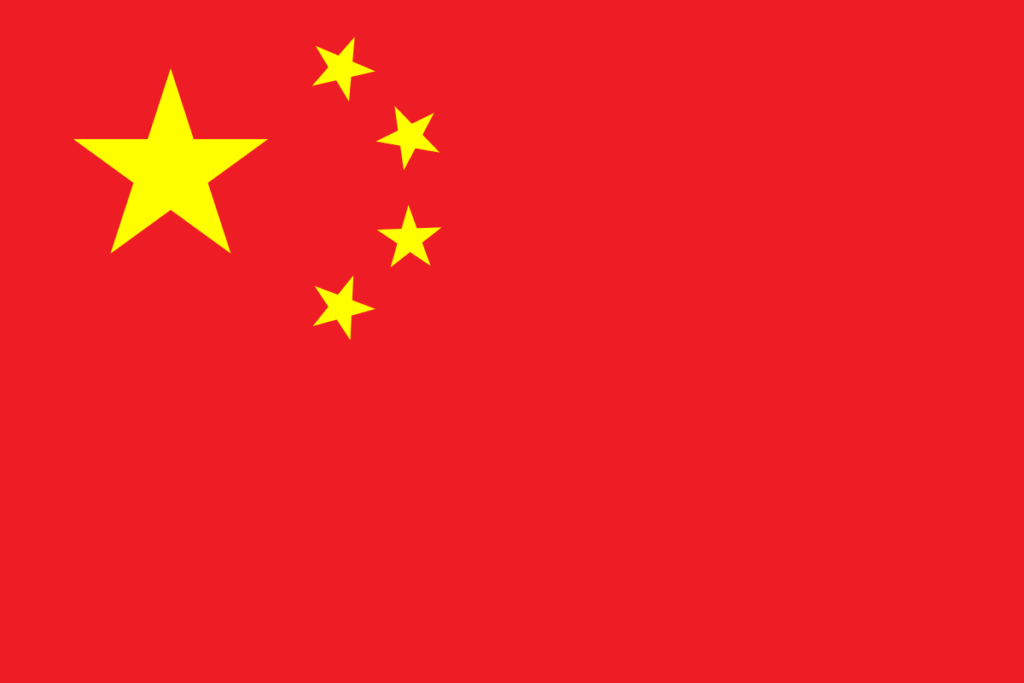
China vs. Southeast Asia: Where Do Europe and US Companies Prefer to Source Metal Manufacturing?
Key Drivers of Asia’s Dominance:
- Cost Efficiency: Lower labor and production costs compared to Western countries.
- Technological Advancements: Increased investment in manufacturing technologies and infrastructure.
- Supply Chain Networks: Proximity to raw materials and robust logistics networks.
- Skilled Workforce: A growing pool of skilled labor in both regions.
While both China and Southeast Asia share these traits, differences in scale, specialization, and geopolitical factors set them apart.
2. Strengths of China in Metal Manufacturing
China remains a dominant force in the global metal manufacturing industry. Its established reputation is backed by decades of industrial growth and unparalleled production capacity.
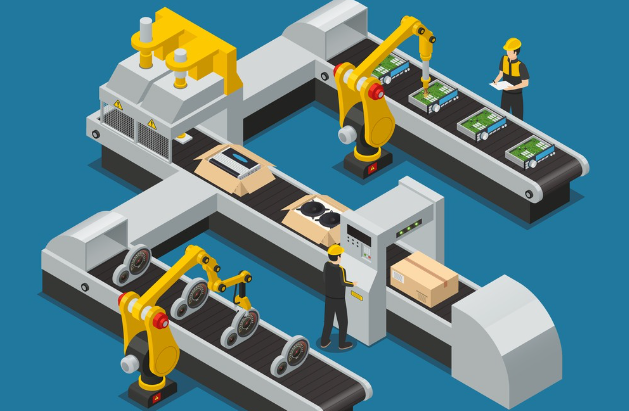
Advantages of Choosing China
- Economies of Scale: China’s ability to handle large-scale production is unmatched. Whether it’s steel fabrication, aluminum extrusion, or precision machining, Chinese manufacturers can deliver high-volume orders efficiently.
- Advanced Technology: The country has heavily invested in automation, robotics, and smart manufacturing. This makes it a top choice for companies requiring high-tech metal components.
- Comprehensive Supply Chains: From raw materials to finished goods, China offers an integrated supply chain ecosystem that simplifies procurement.
- Cost Competitiveness: Despite rising labor costs in recent years, China’s large-scale operations and advanced processes keep prices competitive for bulk orders.
Challenges with Sourcing from China
- Geopolitical Risks: Trade wars, tariffs, and tensions between China and Western countries have prompted businesses to rethink reliance on Chinese suppliers.
- Rising Costs: Labor and operational costs have been climbing, making China less attractive for cost-sensitive buyers.
- IP Concerns: Intellectual property protection remains a concern for some companies.
3. Strengths of Southeast Asia in Metal Manufacturing
Southeast Asia has emerged as a viable alternative to China, with countries like Vietnam, Malaysia, and Thailand leading the charge.
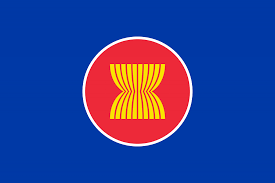
Advantages of Choosing Southeast Asia
- Competitive Costs: Labor costs in Southeast Asia are often lower than in China, particularly in countries like Vietnam and Indonesia. This is a significant draw for cost-sensitive projects.
- Diversification Opportunities: Many Western companies are adopting a “China+1” strategy to reduce dependency on China. Southeast Asia is the natural choice for diversification due to its proximity and growing capabilities.
- Focus on Quality: Manufacturers in countries like Malaysia and Thailand are increasingly recognized for their adherence to international quality standards, such as ISO certifications.
- Political Stability: Many Southeast Asian countries maintain stable trade relations with Europe and the US, minimizing risks associated with tariffs or sanctions.
Challenges with Sourcing from Southeast Asia
- Lower Capacity: While the region is growing, its manufacturing capacity and infrastructure are still catching up with China.
- Fragmented Market: Unlike China’s centralized manufacturing ecosystem, Southeast Asia’s market is spread across multiple countries, making supply chain coordination more complex.
- Limited High-Tech Capabilities: For highly specialized or advanced manufacturing, Southeast Asia may lag behind China’s technological capabilities.
4. Key Factors Influencing the Choice
The decision to source metal manufacturing from China or Southeast Asia often depends on the specific needs of the business. Here are the primary factors that influence this choice:
1. Cost vs. Quality
- China: Best suited for high-volume, cost-sensitive orders where scale outweighs precision.
- Southeast Asia: Ideal for medium-scale orders requiring a balance of cost-efficiency and quality.
2. Product Complexity
- China: Leads in advanced manufacturing processes like CNC machining and robotics-driven production.
- Southeast Asia: Excels in simpler manufacturing needs but is rapidly advancing in precision engineering.
3. Geopolitical Considerations
- China: Trade tensions, particularly with the US, have introduced risks such as tariffs and import restrictions.
- Southeast Asia: Viewed as a neutral and politically stable region with favorable trade agreements.
4. Sustainability
- China: While improving, China’s environmental record can still raise concerns for eco-conscious businesses.
- Southeast Asia: Countries like Malaysia and Thailand are emphasizing sustainable practices, appealing to companies with green goals.
5. Emerging Trends in Metal Manufacturing
1. Shift Towards “China+1” Strategy
Many companies are not abandoning China but are diversifying their supply chains by adding Southeast Asian suppliers. This reduces risk and ensures continuity in case of disruptions.
2. Technological Investments in Southeast Asia
Governments in Southeast Asia are investing in technology and infrastructure to compete with China. For example:
- Malaysia is focusing on precision engineering.
- Vietnam is rapidly becoming a hub for electronics and light metal manufacturing.
3. Focus on Sustainability
Western companies are increasingly prioritizing sustainable and ethical sourcing. Southeast Asia’s growing focus on renewable energy and green manufacturing gives it an edge.
4. Post-Pandemic Resilience
The COVID-19 pandemic exposed vulnerabilities in global supply chains. Businesses now prioritize resilience and may opt for regional suppliers in Southeast Asia to mitigate risks.
6. Conclusion: Which Region Is Right for Your Business?
Choosing between China and Southeast Asia for metal manufacturing depends on your business’s priorities:
- If you need large-scale production with advanced capabilities, China remains a top choice.
- If you value cost-efficiency, diversification, and a focus on quality, Southeast Asia is a strong contender.
Ultimately, many companies adopt a hybrid approach, leveraging the strengths of both regions. As Southeast Asia continues to grow and China evolves its manufacturing landscape, the decision will increasingly depend on the specific needs and strategic goals of the business.
Partner with Lux Metal for Premium Steel Solutions
For businesses seeking high-quality steel products and customized metal solutions, Lux Metal is your trusted partner. Visit our website to explore our wide range of services and see how we can help you meet your industrial needs with precision and excellence.
References
- Evaluating the Rationale and Challenges of Shifting Supply Chains from China to Southeast Asia
- Diversifying global supply chains: Opportunities in Southeast Asia
- De-risking offshore manufacturing: The “China plus” strategy
- The Rise of Chinese Capital: Impact on ASEAN’s Manufacturing Landscape