Introduction
In the world of steel manufacturing and engineering, selecting the right steel grade is crucial to ensuring that products meet specific structural, mechanical, and durability requirements. Among the commonly used grades in various industries are 1008, 1018, and A36 steel. Each of these steel types offers unique characteristics that cater to different applications, and understanding their differences can help manufacturers and engineers make informed decisions.
This article provides a detailed comparison of 1008, 1018, and A36 steel, highlighting their chemical compositions, mechanical properties, common applications, and the advantages and drawbacks of each. Whether you’re involved in automotive, construction, or general fabrication, understanding these steel grades will aid in choosing the most suitable material for your project.
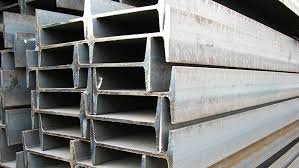
Steel A36
Table of Contents
- Overview of 1008, 1018, and A36 Steel
- Chemical Composition
- Breakdown of carbon content, manganese, and other alloying elements.
- Mechanical Properties
- Tensile strength, yield strength, hardness, ductility, and machinability.
- Manufacturing Processes
- Cold vs. hot rolling and its effect on each grade.
- Applications of 1008, 1018, and A36 Steel
- Comparing the Pros and Cons of 1008, 1018, and A36 Steel
- Key Considerations for Selecting the Right Steel Grade
- Conclusion
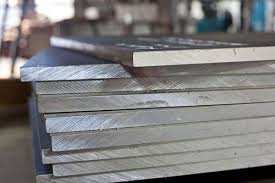
Steel A36
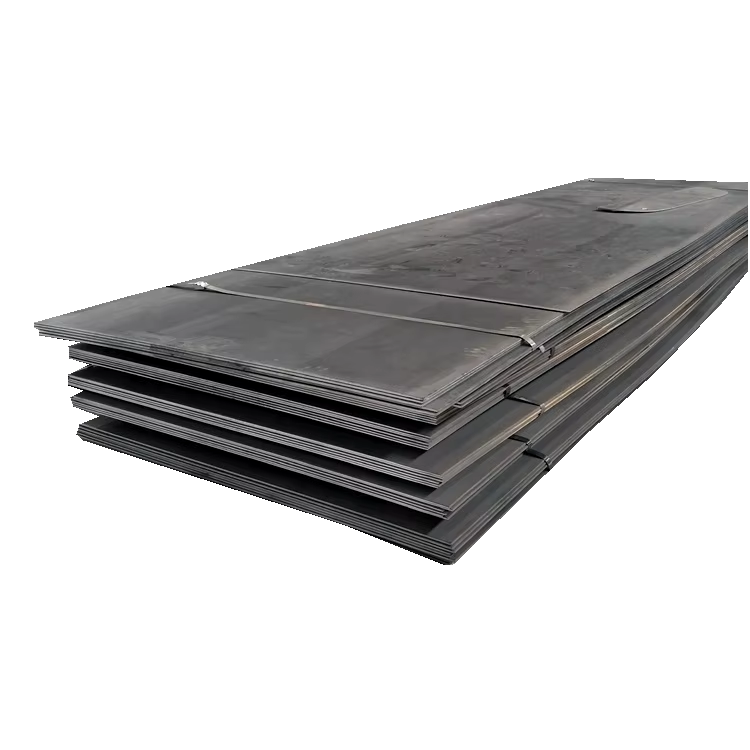
Steel 1008
1. Overview of 1008, 1018, and A36 Steel
To understand the primary distinctions between 1008, 1018, and A36, we need to define each grade and its general uses.
- 1008 Steel: Classified as a low-carbon steel, 1008 is often used for cold-heading applications, where flexibility and ease of machining are essential. It is known for its good formability and weldability.
- 1018 Steel: Another low-carbon steel, 1018 is prized for its balanced strength, machinability, and ductility. It’s commonly used in precision parts, shafts, and structural components where precise dimensions are necessary.
- A36 Steel: A36 falls under the ASTM A36 specification, making it one of the most widely used carbon structural steels. Known for its high strength and excellent weldability, A36 is ideal for structural applications, including building frames, bridges, and heavy equipment.
2. Chemical Composition
The differences in chemical composition between 1008, 1018, and A36 play a significant role in their physical properties and suitability for various applications.
1008 Steel Composition
- Carbon Content: Typically contains 0.10% carbon.
- Manganese: Usually ranges between 0.30% to 0.50%.
- Other Elements: Contains trace amounts of sulfur and phosphorus.
1018 Steel Composition
- Carbon Content: 1018 contains slightly more carbon, typically around 0.18%.
- Manganese: Higher manganese content, around 0.60% to 0.90%, which contributes to its strength.
- Other Elements: Similar to 1008, with trace elements for improved machinability.
A36 Steel Composition
- Carbon Content: Varies up to 0.26%.
- Manganese: Usually ranges between 0.20% to 0.60%.
- Other Elements: Includes trace amounts of copper, phosphorus, and sulfur.
3. Mechanical Properties
Each steel grade exhibits unique mechanical properties due to differences in carbon and manganese content.
1008 Steel Properties
- Tensile Strength: Approximately 440 MPa.
- Yield Strength: Around 210 MPa.
- Ductility: Excellent, with good flexibility, ideal for applications requiring significant bending or shaping.
1018 Steel Properties
- Tensile Strength: Around 620 MPa.
- Yield Strength: Typically 370 MPa.
- Machinability: Known for high machinability, suitable for parts requiring precision.
A36 Steel Properties
- Tensile Strength: Around 400–550 MPa.
- Yield Strength: Typically 250 MPa.
- Weldability: Excellent, making it a top choice for welding-intensive applications.
4. Manufacturing Processes
Steel grades 1008, 1018, and A36 can be manufactured through both cold-rolled and hot-rolled processes, which impact their final mechanical properties.
- Cold Rolling: Often used for 1008 and 1018 to improve surface finish and precision in dimensions. This process also enhances strength by strain hardening.
- Hot Rolling: A36 is typically hot-rolled, which provides a more malleable product with slightly lower precision but greater ease in shaping large structural components.
5. Applications of 1008, 1018, and A36 Steel
Each grade’s unique properties make it suitable for specific applications:
- 1008 Steel: Used in applications where malleability and formability are essential, such as automotive panels, cold-headed fasteners, and wire products.
- 1018 Steel: Common in precision machining, this grade is ideal for manufacturing gears, shafts, spindles, pins, and other components requiring accurate machining and moderate strength.
- A36 Steel: Primarily used in construction, A36 is ideal for beams, frames, and other structural applications. Its high strength and weldability make it a staple in large-scale projects like buildings and bridges.
6. Comparing the Pros and Cons of 1008, 1018, and A36 Steel
Pros and Cons of 1008 Steel
- Pros: Excellent formability and flexibility; highly weldable.
- Cons: Lower strength compared to other carbon steels, limiting it to lighter-duty applications.
Pros and Cons of 1018 Steel
- Pros: Good strength-to-ductility ratio, excellent machinability, suitable for precision applications.
- Cons: Higher cost than A36 and less suitable for heavy structural applications.
Pros and Cons of A36 Steel
- Pros: High strength and weldability, cost-effective for structural applications.
- Cons: Limited ductility compared to 1008 and 1018, making it less suitable for applications requiring significant bending or shaping.
7. Key Considerations for Selecting the Right Steel Grade
When deciding between 1008, 1018, and A36 steel, consider the following factors:
- Strength Requirements: For high-strength applications, A36 may be more suitable, while 1008 is best for light-duty purposes.
- Machinability: For parts requiring precise machining, 1018 is typically the top choice.
- Weldability and Ductility: A36 offers the best weldability for structural applications, while 1008 provides better ductility.
8. Conclusion
In summary, 1008, 1018, and A36 steel each offer unique benefits and limitations that make them ideal for specific applications. Selecting the right grade depends on the requirements for strength, flexibility, weldability, and cost. By understanding the distinct properties of these steel types, engineers and manufacturers can ensure their projects achieve optimal performance, cost-efficiency, and durability.
At LUX Metal, we understand the importance of precision and excellence in metal fabrication. Our expert team and state-of-the-art facilities allow us to tackle even the most challenging projects with confidence. To learn more about our metal fabrication services, visit our website at LUX Metal.
Further Reading
For more insights on metal fabrication, check out these resources: