When it comes to stainless steel, two of the most commonly used grades are 304 and 316. These grades are widely recognized for their durability, corrosion resistance, and versatility across various industries. However, each has specific characteristics that make it more suitable for certain applications than others. Understanding the differences between Stainless Steel 304 and 316 can help you make an informed decision for your project, ensuring optimal performance and longevity. In this article, we will delve into the composition, properties, advantages, applications, and cost considerations of these two popular stainless steel grades.
1. Overview of Stainless Steel
Stainless steel is a metal alloy primarily composed of iron, chromium, and other elements such as nickel, manganese, and molybdenum. Its defining characteristic is its resistance to corrosion, which results from a protective oxide layer that forms on its surface when exposed to oxygen. This makes stainless steel highly valuable across industries like construction, automotive, medical, and food processing, where durability and hygiene are essential.

Types of Stainless Steel:
Stainless steel is categorized into different families based on its crystal structure and chemical composition. The main types include:
- Austenitic Stainless Steel: Contains high levels of chromium and nickel, known for excellent corrosion resistance and workability.
- Ferritic Stainless Steel: Magnetic, with moderate corrosion resistance, often used in automotive and industrial applications.
- Martensitic Stainless Steel: Known for high strength and hardness, but with limited corrosion resistance.
- Duplex Stainless Steel: Combines austenitic and ferritic properties, offering higher strength and corrosion resistance.
304 and 316 stainless steels are both part of the austenitic family, offering excellent corrosion resistance and formability, making them ideal for many applications.
2. Composition of Stainless Steel 304 and 316
The differences between 304 and 316 stainless steel largely stem from their distinct chemical compositions.
Stainless Steel 304:
- Chromium: 18-20%
- Nickel: 8-10.5%
- Carbon: Up to 0.08%
- Other Elements: Small amounts of manganese, silicon, and phosphorus
Stainless Steel 304, also known as “18/8” stainless steel due to its 18% chromium and 8% nickel content, is a general-purpose stainless steel grade with excellent corrosion resistance, formability, and weldability.
Stainless Steel 316:
- Chromium: 16-18%
- Nickel: 10-14%
- Molybdenum: 2-3%
- Carbon: Up to 0.08%
316 stainless steel is similar in composition to 304 but includes an additional 2-3% molybdenum, which enhances its corrosion resistance, particularly against chlorides and other harsh chemicals.
3. Key Properties Comparison: 304 vs. 316 Stainless Steel
Let’s examine how the composition differences impact the physical and mechanical properties of 304 and 316 stainless steel.
Corrosion Resistance:
- 304 Stainless Steel: Offers excellent resistance to oxidation and corrosion under normal atmospheric conditions. It can withstand various acidic environments but may corrode in highly saline environments or when exposed to chloride.
- 316 Stainless Steel: Due to the addition of molybdenum, 316 stainless steel has superior corrosion resistance, especially in chlorinated and saline environments. It is often chosen for marine applications and industries involving harsh chemicals.
Strength and Hardness:
- 304 Stainless Steel: Has a tensile strength of around 505 MPa and good hardness but is not as strong as 316.
- 316 Stainless Steel: Generally exhibits higher tensile strength and hardness than 304 due to the presence of molybdenum, making it suitable for heavy-duty applications.
Heat Resistance:
- 304 Stainless Steel: Capable of withstanding high temperatures, making it suitable for applications involving prolonged exposure to heat. It performs well up to 870°C (1598°F) under continuous service and up to 925°C (1697°F) in intermittent service.
- 316 Stainless Steel: Offers slightly better heat resistance, which can benefit specific applications that demand stability in high-temperature environments.
Magnetism:
- Both 304 and 316 stainless steels are non-magnetic in their annealed states, though they may exhibit some magnetic properties when cold-worked.
Formability and Weldability:
- 304 Stainless Steel: Known for excellent formability and weldability, making it suitable for complex shapes.
- 316 Stainless Steel: While still highly formable and weldable, the added molybdenum can sometimes affect weld quality, though this can usually be managed with proper technique and post-weld treatments.
4. Applications of Stainless Steel 304 and 316
The choice between 304 and 316 often comes down to environmental factors, cost considerations, and specific application requirements.
Stainless Steel 304 Applications:
- Kitchen Equipment: Used in sinks, cookware, and appliances due to its corrosion resistance, ease of cleaning, and aesthetic appeal.
- Architectural and Structural Applications: Widely used in buildings, railings, and industrial structures.
- Food and Beverage Industry: Commonly used for food-grade containers, processing equipment, and storage tanks, as it does not impart flavors and is safe for contact with food.
- Automotive Parts: Found in car trim, exhaust components, and decorative accessories.
Stainless Steel 316 Applications:
- Marine Industry: Due to its resistance to chloride-induced corrosion, 316 is ideal for marine environments, such as boat fittings, propeller shafts, and underwater equipment.
- Pharmaceutical and Medical Devices: Used in medical implants, surgical instruments, and drug manufacturing due to its corrosion resistance and biocompatibility.
- Chemical Processing and Storage: Used in tanks, pumps, and pipelines for handling corrosive chemicals, including acids and salts.
- Oil and Gas Industry: Commonly used in offshore rigs, pipelines, and equipment that may be exposed to seawater and high temperatures.
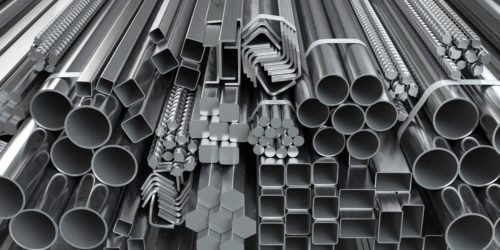
5. Cost Considerations
One of the primary factors influencing the choice between 304 and 316 stainless steel is cost. Stainless Steel 316 is generally more expensive than 304 due to the added cost of molybdenum. This difference can impact project budgets, especially in large-scale applications. Therefore, choosing 316 stainless steel is often justified only when enhanced corrosion resistance or strength is required, making it cost-effective in demanding environments.
6. Choosing Between 304 and 316 Stainless Steel: Key Factors
1. Corrosive Environment:
If your project involves exposure to salty or chlorinated environments, 316 is the better option due to its molybdenum content. For instance, in coastal architecture or pool equipment, 316 can prevent premature corrosion and ensure a longer lifespan.
2. Temperature Tolerance:
For high-temperature applications, both grades are suitable, but 316’s marginally better heat resistance could be advantageous in prolonged high-heat environments.
3. Cost Efficiency:
If your project does not require high chloride resistance, Stainless Steel 304 may be the more economical choice. It provides excellent performance in most conditions, making it an efficient option for budget-conscious applications.
4. Industry Standards and Regulations:
In industries like food, medical, and pharmaceutical, specific regulations often require particular stainless steel grades. In many cases, 316 stainless steel is preferred or mandated to meet health, safety, and durability standards.
5. Aesthetic Requirements:
For decorative purposes where corrosion resistance is not critical, 304 stainless steel often suffices. However, in more aggressive environments where aesthetic preservation over time is necessary, 316 may be worth the investment.
7. Maintenance and Care
Both 304 and 316 stainless steels are low-maintenance, but proper care can extend their life and aesthetic appeal. Here are a few tips:
- Regular Cleaning: Especially in harsh environments, regular cleaning prevents salt buildup and other contaminants that could lead to surface damage.
- Avoid Harsh Chemicals: Chlorine-based cleaners can damage stainless steel. Use mild detergents or specialized stainless steel cleaners.
- Prevent Scratches: Both grades are durable but can be scratched by abrasive materials. Use soft cloths for cleaning to preserve the surface finish.
8. Conclusion
Stainless Steel 304 and 316 are both high-quality materials with distinct advantages and specific applications. While 304 stainless steel is versatile and suitable for many general-purpose applications, 316 stainless steel is often preferred in harsher environments due to its enhanced corrosion resistance. The choice between the two ultimately depends on the environment, application demands, and budget considerations.
Understanding the properties of each type can help you make an informed choice, ensuring your project achieves both functionality and durability. Whether for a kitchen appliance, medical device, or marine equipment, selecting the right stainless steel grade is essential for long-term success and performance.
At LUX Metal, we understand the importance of precision and excellence in metal fabrication. Our expert team and state-of-the-art facilities allow us to tackle even the most challenging projects with confidence. To learn more about our metal fabrication services, visit our website at LUX Metal.
Further Reading
For more insights on metal fabrication, check out these resources: