Why Reducing Labor Costs is Crucial for Manufacturing
Labor is one of the highest costs in manufacturing. It includes wages, benefits, training expenses, and compliance costs, all of which can quickly add up. As manufacturers deal with tighter budgets, a competitive labor market, and rising supply chain expenses, implementing efficient labor cost-reduction strategies is essential. However, cutting labor costs should not compromise product quality, lead times, or workplace safety. The following approaches can support manufacturers in achieving a balanced strategy to manage costs effectively.
1. Investing in Automation and Technology
Modern manufacturing automation, including robotics, machine learning, and artificial intelligence, offers promising avenues for reducing labor costs. Automation can handle repetitive, low-skill tasks, freeing human workers for higher-value tasks such as quality control, innovation, and customer engagement.
Investing in advanced technology can yield immediate returns by decreasing the number of labor hours needed for certain processes and minimizing human error. Moreover, incorporating tools such as AI-driven data analytics allows manufacturers to streamline workflows, anticipate equipment failures, and enhance supply chain forecasting.
Automation in Practice
Consider adopting cobots (collaborative robots), which are increasingly popular in smaller manufacturing plants. These robots work alongside human operators to perform tasks like assembly, material handling, and welding. Cobots are ideal for companies that want to scale up automation without the substantial investments required by larger robotic systems.
2. Lean Manufacturing Principles
Lean manufacturing, a methodology developed by Toyota, focuses on minimizing waste without sacrificing productivity. By implementing lean principles, manufacturers can significantly reduce labor costs associated with redundant processes and excess inventory.
Key lean practices include:
- Just-In-Time (JIT) Production: JIT reduces inventory costs by producing goods only when there is demand, eliminating the need to store excess products and materials.
- Value Stream Mapping: Identifying waste in the production process, from design to delivery, helps streamline operations, reduce labor inefficiencies, and improve overall workflow.
Lean manufacturing helps reduce operational costs by optimizing workforce allocation, decreasing time spent on unnecessary tasks, and focusing labor efforts where they add the most value.
3. Optimize Workforce Management
Effective workforce management is another key factor in controlling labor costs. By carefully planning shift schedules, cross-training employees, and using time-tracking software, manufacturers can optimize productivity and avoid costly overtime.
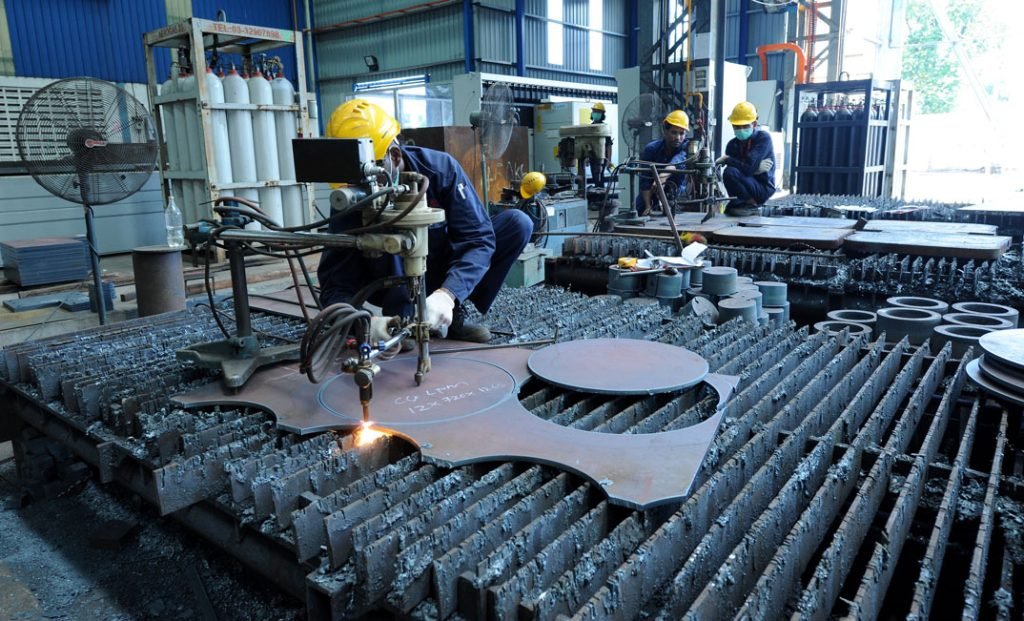
Strategies for Workforce Optimization
- Shift Scheduling Software: Automating the scheduling process with software that takes into account peak demand times, employee availability, and labor laws can significantly reduce unnecessary labor costs.
- Cross-Training Employees: A cross-trained workforce provides greater flexibility, allowing employees to cover multiple tasks or roles. This versatility minimizes downtime and can reduce the need to hire additional workers for specific tasks, especially during peak seasons.
Tracking labor data can also identify areas where labor is being underutilized or overextended, enabling manufacturers to make adjustments that lead to cost savings without sacrificing productivity.
4. Implementing Preventive Maintenance Programs
Unexpected equipment breakdowns can lead to costly downtime and labor-intensive repairs. Implementing preventive maintenance schedules can keep machinery running smoothly and reduce labor costs by preventing disruptions.
Preventive Maintenance Benefits
- Reduced Downtime: Preventive maintenance keeps equipment in optimal condition, reducing the risk of unexpected breakdowns.
- Labor Efficiency: When machines are well-maintained, fewer labor hours are required for emergency repairs and troubleshooting.
- Cost Savings on Parts: Preventive maintenance helps avoid expensive repairs by catching minor issues before they escalate.
Regular maintenance schedules are essential, especially in industries where machinery is in constant use. Predictive maintenance solutions, powered by IoT technology, can alert technicians to issues before they affect production, making it easier to maintain optimal equipment performance with minimal labor interruptions.
5. Outsource Non-Core Tasks
Outsourcing non-core tasks, such as IT support, janitorial services, and some administrative functions, can help manufacturing companies focus their labor resources on essential operations. By outsourcing, companies can reduce overhead costs associated with full-time staff, such as benefits and training, and allocate those resources to core manufacturing tasks that directly impact profitability.
How to Decide What to Outsource
- Evaluate Core Competencies: Focus on in-house processes that give your company a competitive advantage and outsource other tasks.
- Consider Flexibility Needs: If your production fluctuates seasonally, outsourcing can provide more flexibility than hiring full-time staff.
6. Utilize Data Analytics to Drive Efficiency
Data analytics is a valuable tool for identifying inefficiencies in labor management. By analyzing production data, companies can uncover trends that indicate where labor hours are being overused, where overtime is most prevalent, or which tasks are consuming too much time.
Data-Driven Labor Insights
- Workforce Allocation: Use analytics to allocate labor based on demand forecasts, reducing the likelihood of overstaffing or understaffing.
- Performance Metrics: Tracking metrics like average labor hours per unit produced can help managers identify high-performing teams and areas that need improvement.
Real-time data analysis can empower companies to make informed decisions, prevent bottlenecks, and continuously improve productivity, thus reducing labor costs.
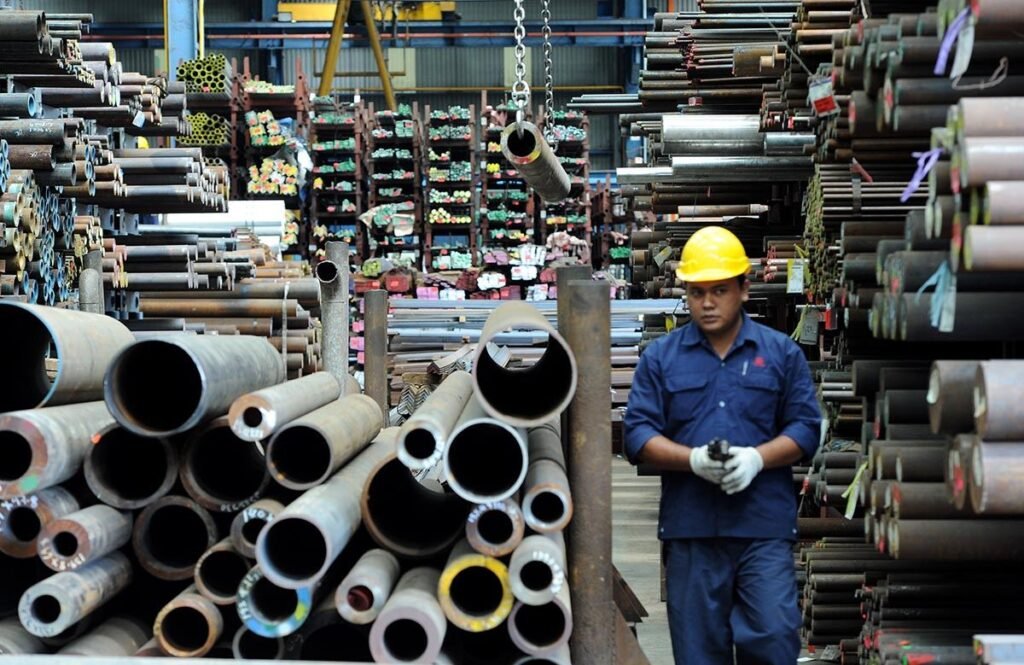
7. Enhance Employee Retention
High employee turnover is costly, as hiring and training new employees require significant time and resources. By fostering a supportive and rewarding workplace culture, manufacturers can improve employee retention and reduce the costs associated with labor turnover.
Retention Strategies
- Offer Competitive Compensation: Fair wages, benefits, and performance bonuses can improve employee satisfaction and retention.
- Promote Career Development: Training programs and clear advancement paths can encourage employees to stay longer, reducing the need for new hires.
- Focus on Workplace Safety: Ensuring a safe and comfortable working environment demonstrates care for employee well-being and can boost morale.
Investing in employees by offering training programs and opportunities for advancement can yield long-term savings by reducing turnover and the expenses associated with training new hires.
8. Streamline Supply Chain Management
Effective supply chain management minimizes delays, reduces excess inventory, and prevents labor costs related to managing unnecessary stock. Streamlining the supply chain ensures that labor resources are used efficiently and lowers production costs.
Effective Supply Chain Strategies
- Supplier Relationships: Maintain strong relationships with suppliers to ensure consistent quality and on-time delivery of materials.
- Inventory Management Software: Implement software that provides real-time visibility into inventory levels to avoid overproduction or understocking.
An efficient supply chain reduces the amount of time and labor required for inventory handling, freeing up resources for core production activities.
Conclusion
Reducing labor costs is crucial for manufacturers seeking long-term profitability and growth in a highly competitive industry. By investing in automation, adopting lean manufacturing principles, optimizing workforce management, and utilizing data analytics, manufacturers can strategically reduce costs without sacrificing quality or productivity. These methods help build a resilient, agile workforce prepared to meet the demands of modern manufacturing.
For manufacturing companies in Malaysia seeking high-quality, customized metal solutions, Lux Metal offers a full suite of stainless steel fabrication services designed to enhance efficiency and meet the rigorous standards of today’s market.