What is Aluminum Die Casting?
Aluminum die casting is a manufacturing process where molten aluminum is forced under high pressure into a mold cavity, or “die,” to create intricately shaped components. Due to aluminum’s lightweight and excellent corrosion resistance, die casting is especially useful for parts that need to withstand high stress without excessive weight. This process produces strong, durable parts with minimal machining, making it ideal for both large production runs and complex designs.
Aluminum Casting Market Outlook: Size and Growth Forecast
According to the Aluminum Casting Global Market Report 2024, the aluminum casting market has shown significant growth in recent years. The market size increased from $65.53 billion in 2023 to $70.76 billion in 2024, reflecting a compound annual growth rate (CAGR) of 8.0%. This growth has been driven by rapid economic development, infrastructure expansion, and the rising demand for sustainable and eco-friendly construction materials. Increased urbanization and industrialization have further contributed to the market’s expansion.
Looking forward, the aluminum casting market is expected to maintain strong growth, with projections indicating it will reach $94.46 billion by 2028, at a CAGR of 7.5%. Key factors fueling this growth include the rise in electric vehicle production, renewable energy infrastructure, and a global shift towards a circular economy. Technological advancements in casting processes, integration of additive manufacturing, and digitalization in casting simulation are also anticipated to drive market expansion, along with customization and design complexity in alloy development.
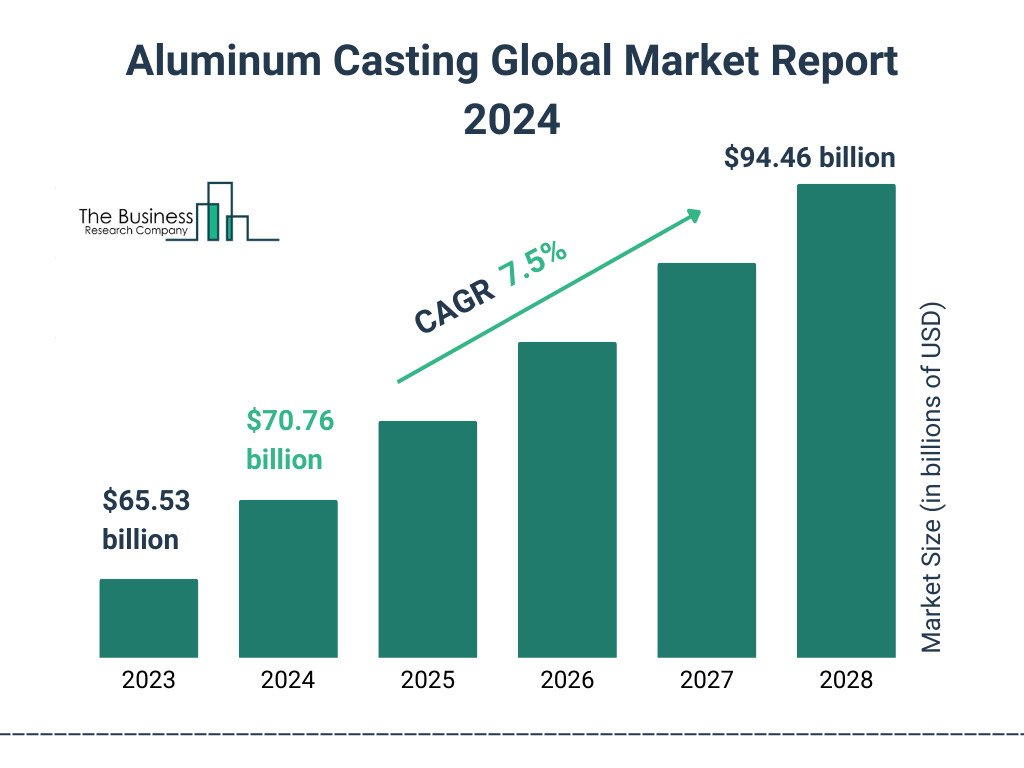
6 Key Things to Know About Aluminum Die Casting
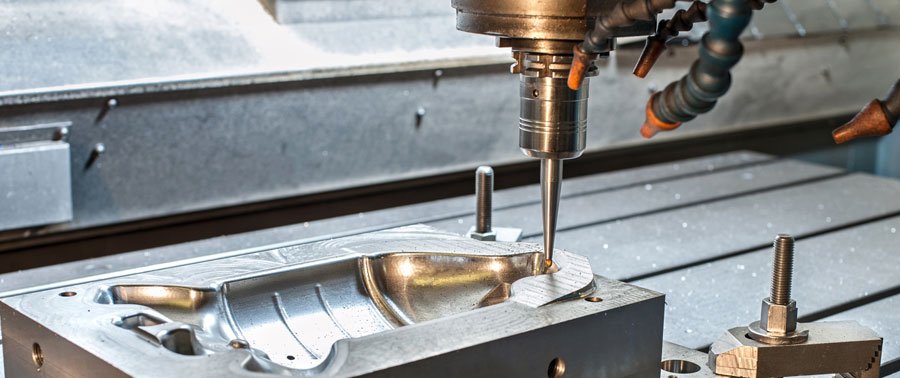
1. High-Quality Surface Finish and Precision
Aluminum die casting offers exceptional surface quality and precision in every part it produces. The high-pressure injection of molten aluminum into a die allows for tight tolerances and intricate details. This precision reduces the need for additional machining, saving both time and resources. The resulting parts have a smooth finish, which can be further treated or coated, making them suitable for visible or structural applications in industries like automotive and consumer electronics.
2. Cost-Effective for Large Production Runs
One of the most significant advantages of aluminum die casting is its cost-effectiveness for high-volume production. Once the die (mold) is created, it can be used repeatedly, making it a practical choice for large-scale manufacturing. While the initial investment in tooling can be high, the per-part cost drops significantly as the production volume increases. This scalability makes die casting a preferred method for industries requiring consistent, large-batch production, as it minimizes costs while maintaining part quality.
3. Excellent Strength-to-Weight Ratio
Aluminum’s strength-to-weight ratio makes it an ideal material for parts requiring durability without added weight. Die-cast aluminum components are strong yet lightweight, giving them an advantage in applications where performance and fuel efficiency are priorities, such as in the automotive and aerospace industries. This strength-to-weight advantage helps products meet performance standards without compromising on efficiency or durability.
4. Versatility in Design and Applications
Die casting allows manufacturers to produce a wide range of complex shapes with minimal additional tooling. Whether creating detailed geometries for intricate machine parts or structural components for heavy-duty applications, aluminum die casting provides excellent design flexibility. This versatility extends to customization options, as the process supports the integration of unique features, such as threaded inserts, bosses, and complex geometries, making it suitable for diverse applications.
5. Fast Production Cycle Times
Aluminum die casting is characterized by fast production cycle times, allowing manufacturers to quickly turn around high volumes of components. The rapid cooling of aluminum once injected into the mold enables shorter cycle times compared to other methods, such as sand casting. This efficiency is crucial for meeting tight deadlines in competitive markets, making aluminum die casting an attractive option for manufacturers aiming to maintain a swift pace without sacrificing quality.
6. Eco-Friendly Manufacturing Process
The aluminum die casting process is not only efficient but also environmentally friendly. Aluminum is highly recyclable, and the die casting process generates minimal waste compared to other manufacturing techniques. This sustainable approach aligns with growing industry standards and consumer preferences for environmentally responsible practices. Manufacturers can confidently promote their use of aluminum die casting as part of a commitment to sustainability while benefiting from reduced material costs associated with recycling.
Advantages of Aluminum Die Casting
Aluminum die casting has become a popular choice for numerous reasons, thanks to its unique properties and benefits. Some of the notable advantages include:
- Corrosion Resistance: Aluminum die-cast parts exhibit excellent resistance to corrosion, which extends their lifespan and reduces maintenance needs in harsh environments. This characteristic makes aluminum particularly suitable for outdoor applications and environments prone to moisture and corrosion.
- Thermal Conductivity: Aluminum is a good thermal conductor, making it ideal for parts that dissipate heat, such as those used in electronic and lighting applications. This thermal efficiency helps maintain optimal operating conditions for electronic devices, improving performance and reliability.
- Recyclability: Aluminum is 100% recyclable, which aligns with sustainable manufacturing practices and reduces the environmental impact. The ability to recycle aluminum without losing its properties ensures a continuous cycle of material use, appealing to eco-conscious consumers and manufacturers alike.
- Dimensional Stability: Parts produced through die casting retain their shape over time, providing stability even in high-temperature applications. This dimensional stability contributes to the overall quality and reliability of the final product, particularly in precision applications where maintaining tolerances is critical.
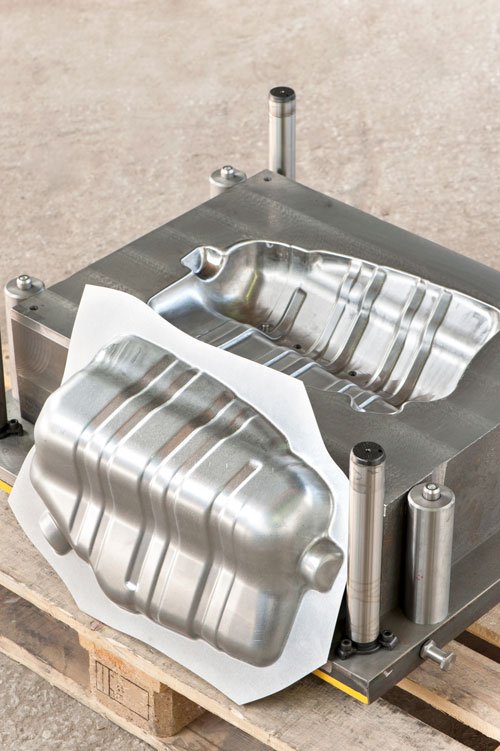
Applications Across Multiple Industries
Aluminum die casting’s versatility makes it an ideal choice for various applications across multiple industries. Below are some key sectors where aluminum die casting plays a vital role:
1. Automotive Industry
Aluminum die casting is extensively used in the automotive sector due to its lightweight and high-strength characteristics. Key applications include:
- Engine Components: Aluminum die-cast parts are commonly used for engine blocks, cylinder heads, and oil pans. Their lightweight nature helps improve fuel efficiency while maintaining structural integrity.
- Transmission Housings: Many vehicles utilize aluminum die-cast transmission cases, which offer excellent strength-to-weight ratios, reducing overall vehicle weight and enhancing performance.
- Suspension Parts: Aluminum die casting is also applied in manufacturing suspension components, such as control arms and brackets. These parts benefit from aluminum’s ability to absorb shocks while keeping the weight down.
- Structural Elements: Components like crossmembers, support brackets, and underbody shields are produced using aluminum die casting, contributing to vehicle rigidity and safety.
2. Electronics Industry
The electronics sector relies heavily on aluminum die casting for its unique properties and functional requirements:
- Heat Sinks: Aluminum is an excellent thermal conductor, making it ideal for heat sink applications. Die-cast aluminum heat sinks help dissipate heat from electronic components, ensuring they operate within safe temperature ranges.
- Enclosures and Housings: Die-cast aluminum enclosures protect sensitive electronic devices from environmental factors. These enclosures are lightweight, durable, and often aesthetically pleasing, making them suitable for consumer electronics, telecommunications equipment, and industrial devices.
- Connectors and Components: Many electrical connectors and components are produced through aluminum die casting, benefiting from the material’s strength, conductivity, and corrosion resistance.
3. Consumer Goods
Aluminum die casting has become increasingly popular in the consumer goods sector, where aesthetics and durability are essential:
- Kitchen Appliances: Items such as cookware, blenders, and food processors often feature die-cast aluminum components, which provide durability and a polished finish that appeals to consumers.
- Furniture Fittings: Aluminum die-cast parts are commonly used in furniture hardware, such as brackets, legs, and decorative elements. The lightweight nature of aluminum helps create stylish yet functional designs.
- Sporting Goods: Many sporting goods, such as bicycle frames, helmets, and tools, utilize aluminum die casting for its lightweight properties and durability, enhancing performance and user experience.
4. Machinery and Equipment
Aluminum die casting is essential in various industrial machinery applications:
- Construction Equipment: Components like hydraulic cylinders, frames, and gears used in construction machinery often employ aluminum die casting due to its strength and resistance to wear.
- Agricultural Machinery: Many agricultural implements, such as tractors and harvesters, utilize die-cast aluminum parts. This reduces weight while maintaining strength, improving fuel efficiency and ease of use.
- Manufacturing Tools: Tooling and machinery parts, such as casings, housings, and supports, benefit from the precision and durability offered by aluminum die casting. This enhances the overall performance of manufacturing equipment.
5. Aerospace Industry
In the aerospace sector, aluminum die casting is vital for producing lightweight yet strong components:
- Aircraft Structures: Components such as fuselage frames, bulkheads, and fairings are often manufactured using aluminum die casting, contributing to overall weight reduction without sacrificing strength.
- Engine Components: Die-cast aluminum parts are used in various aircraft engine components, including housings and brackets. The lightweight properties help improve fuel efficiency and overall performance.
- Interior Components: Aluminum die-cast parts can also be found in aircraft interiors, including structural supports, trays, and other fixtures that require lightweight yet durable materials.
6. Marine Applications
Aluminum die casting is increasingly popular in the marine industry, where components are exposed to harsh environments:
- Boat Fittings: Items such as cleats, hinges, and brackets often use die-cast aluminum for its corrosion resistance and strength, ensuring longevity in saltwater conditions.
- Outboard Motor Components: Many outboard motors utilize die-cast aluminum parts, which provide necessary strength while reducing overall weight for better performance.
- Marine Hardware: Various hardware components used in boats, such as steering wheels and throttle controls, are often made from die-cast aluminum, combining aesthetic appeal with functional durability.
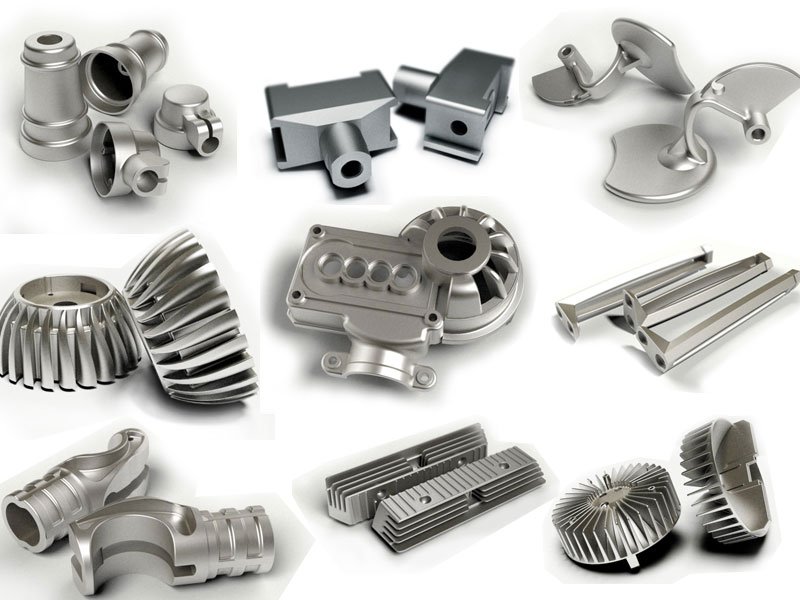

Conclusion
Aluminum die casting is a versatile manufacturing process that plays a crucial role in a wide array of industries. From automotive to electronics and beyond, the unique properties of aluminum make it an ideal choice for producing high-quality, reliable, and lightweight components. As manufacturers continue to seek innovative solutions for their production needs, aluminum die casting stands out as a reliable method that combines efficiency with exceptional results.
For further insights on aluminum die casting and to explore how it can benefit your next project, visit Lux Metal for professional services and customized solutions that cater to your specific requirements.
For additional information, check out these resources: