What Is Metal Fabrication?
Metal fabrication is the process of cutting, shaping, and assembling metal materials to create products or structures. This process encompasses a wide range of methods and techniques, including cutting, bending, welding, forming, and assembling. Metal fabricators work with different types of metal, including steel, aluminum, copper, and alloys, depending on the specific project requirements.
Key Steps in the Metal Fabrication Process
The metal fabrication process generally follows these steps to ensure high-quality output and accurate results:
- Design and Engineering: Before beginning fabrication, detailed blueprints and CAD (Computer-Aided Design) models are created to ensure precision. These designs help fabricators visualize the final product and determine the best fabrication techniques.
- Cutting: Metal sheets or bars are cut to specified dimensions. This is typically done using equipment like laser cutters, plasma cutters, or water jets for high precision.
- Bending and Forming: Once cut, the metal may be bent or formed to match the design requirements. Bending machines or press brakes are used to create various shapes.
- Welding and Assembly: Different parts are welded together to form the final structure. This stage is crucial for creating a strong, cohesive structure.
- Surface Treatment and Finishing: Surface treatments, like powder coating or painting, are applied to enhance the durability and aesthetic appeal of the product.
- Quality Control: Fabricators thoroughly inspect the final product to ensure it meets all specifications and quality standards.
Applications of Metal Fabrication
Metal fabrication has widespread applications in multiple industries. Here are a few common uses:
- Automotive Industry: Metal fabrication is crucial in manufacturing parts like frames, engine components, and exhaust systems.
- Construction: Structural beams, railings, staircases, and various support structures in buildings are fabricated metal parts.
- Aerospace: Metal fabrication creates precise parts for aircraft, including engine components, frames, and landing gear.
- Industrial Equipment: Metal fabrication is used to produce machinery, tools, and industrial equipment parts.
- Consumer Goods: Metal parts in electronics, appliances, and even furniture are fabricated for durability and functionality.
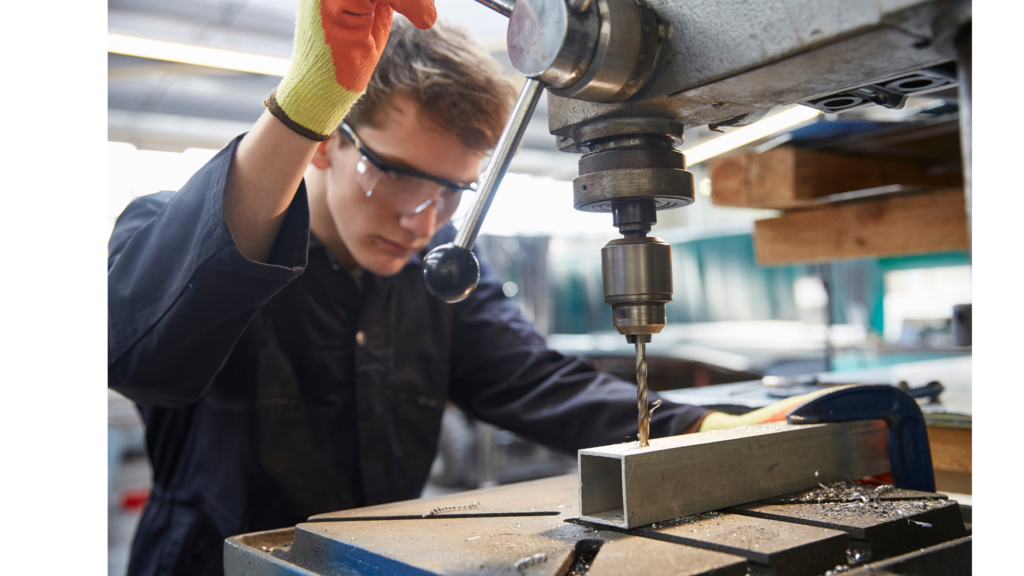
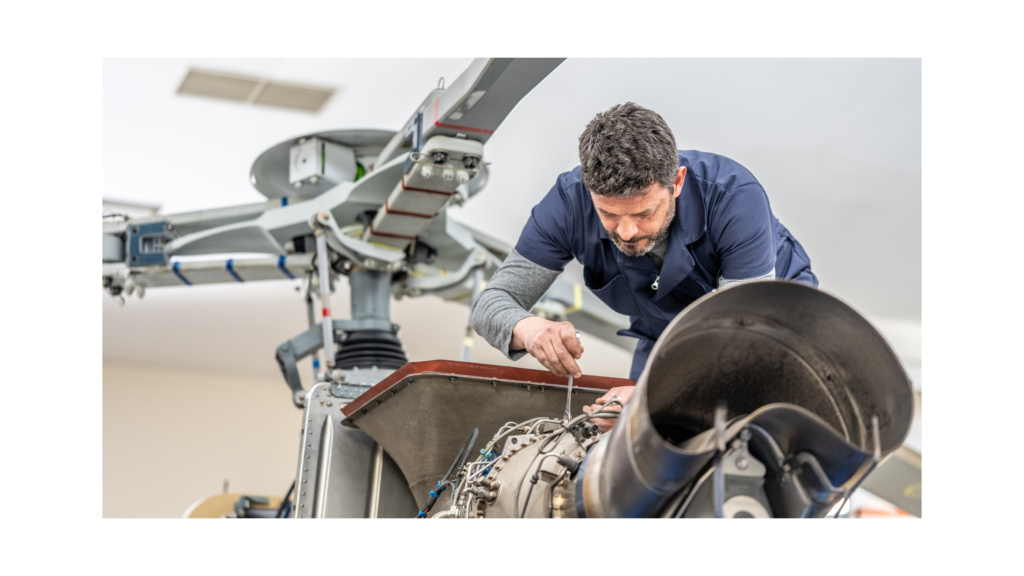
5 Common Metal Fabrication Mistakes to Avoid
Even with advanced tools and technologies, metal fabrication projects can face setbacks if certain mistakes are made. Here are five of the most common errors and how to avoid them for a smoother workflow and higher quality outcomes.
1. Inadequate Planning and Design
Why It Matters: Proper planning and design are the foundation of any successful metal fabrication project. Without a clear and detailed design, fabricators may face unexpected challenges during production, leading to errors, wasted materials, and delays.
Common Issues:
- Misaligned Parts: Parts that don’t fit together as planned, leading to rework.
- Design Overlooked for Assembly: Components might look fine individually but could be hard to assemble.
- Material Choice Errors: Using a material that is unsuitable for the intended application can lead to structural failures.
Example: Imagine a project where a team needs to fabricate metal parts for an industrial machine. Due to inadequate planning, they realize mid-project that some parts are oversized and won’t fit into the machine. This oversight leads to redoing the work, wasting both time and resources.
How to Avoid It:
- Utilize CAD software for detailed design and 3D modeling to identify potential issues before fabrication begins.
- Collaborate closely with engineers and clients to align on design specifications.
- Double-check material choices for compatibility with project requirements.
Tip: Using software like SolidWorks or AutoCAD can help identify design flaws early, allowing for a smoother production process.
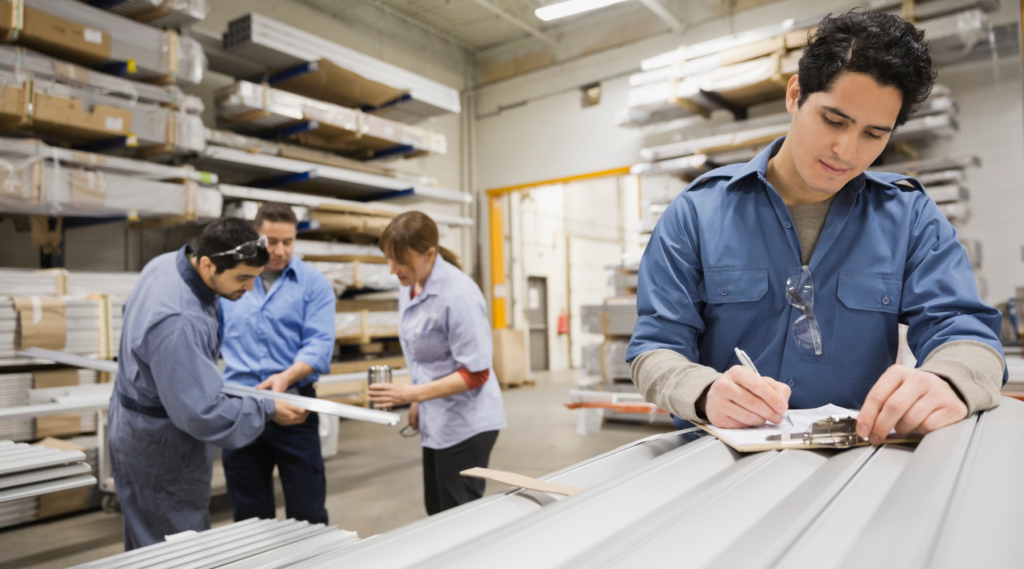
2. Incorrect Material Handling and Storage
Why It Matters: Metals are susceptible to various environmental factors like humidity, temperature, and chemical exposure. Poor handling and storage can lead to material degradation, impacting the final product’s quality and durability.
Common Issues:
- Corrosion and Oxidation: Exposing metals like steel to moisture can cause rust, weakening the material.
- Deformation: Improper stacking or storing heavy metals can lead to warping or bending.
- Surface Contamination: Dust, oil, or other contaminants on metal surfaces can affect finishes and coatings.
Example: A construction company stored steel beams outside, without adequate cover, resulting in surface rust. When they finally used these beams, additional time and effort were required to clean and treat the surfaces, adding unnecessary costs to the project.
How to Avoid It:
- Store metals in a controlled environment, away from moisture and extreme temperatures.
- Organize storage to prevent stacking heavy materials on softer ones.
- Implement proper handling procedures to avoid unnecessary bending or scratching.
Tip: Use protective coatings or corrosion inhibitors when storing metal for extended periods, particularly if environmental conditions aren’t ideal.
3. Inaccurate Measurements and Cuts
Why It Matters: Precision is key in metal fabrication, where even a small deviation in measurements can lead to significant issues during assembly. Inaccurate cuts result in parts that don’t fit, leading to wasted materials and time.
Common Issues:
- Miscalculated Dimensions: Incorrect dimensions can prevent components from fitting together correctly.
- Poor Cutting Technique: Using the wrong tools or techniques can cause jagged or uneven edges.
- Tool Wear and Tear: Dull or damaged cutting tools can lead to inaccurate cuts.
Example: A manufacturer fabricates parts for an HVAC system, but due to slight miscalculations, the ductwork sections don’t align properly. The team has to redo the cuts, which delays the project and incurs additional costs.
How to Avoid It:
- Use precise measuring tools, such as digital calipers, laser measuring systems, and CNC machines.
- Regularly calibrate and maintain cutting tools to ensure accuracy.
- Implement a double-check system to verify all measurements before cutting.
Tip: For complex shapes or intricate cuts, consider using laser cutting or water jet cutting, as these methods offer high precision and minimize human error.
4. Improper Welding Techniques
Why It Matters: Welding is a crucial step in metal fabrication, and improper techniques can compromise the structural integrity of the final product. Issues like poor weld penetration, incorrect electrode choice, and improper welding speeds can lead to weak joints and potential product failure.
Common Issues:
- Cold Welding: Occurs when the welding heat is insufficient, resulting in poor penetration and weak bonds.
- Overheating: Excessive heat can lead to warping or a brittle weld that’s prone to cracking.
- Inconsistent Weld Beads: Inconsistent welding can create uneven surfaces, leading to structural weaknesses.
Example: In a structural steel fabrication project, an inexperienced welder fails to achieve proper penetration in a load-bearing joint. During quality inspection, the weak welds are identified, requiring rework and potentially delaying the project completion.
How to Avoid It:
- Ensure welders are well-trained and familiar with the specific materials and welding methods required.
- Choose the appropriate welding technique, whether MIG, TIG, or arc welding, based on the project’s needs.
- Conduct regular quality checks to detect welding inconsistencies early.
Tip: Consider investing in robotic welding for high-precision and high-volume projects. Robots ensure consistent weld quality, especially for repetitive tasks.
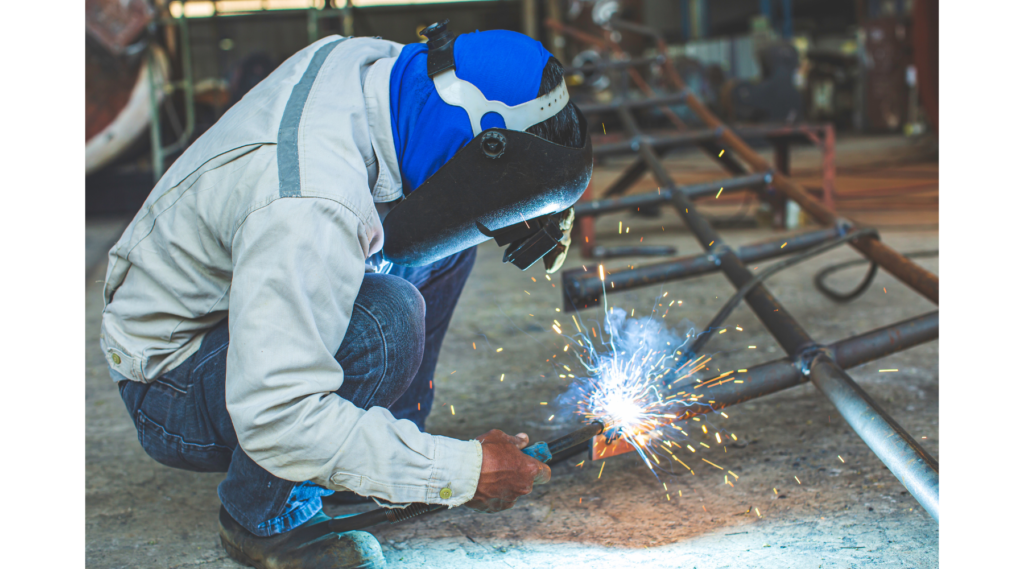
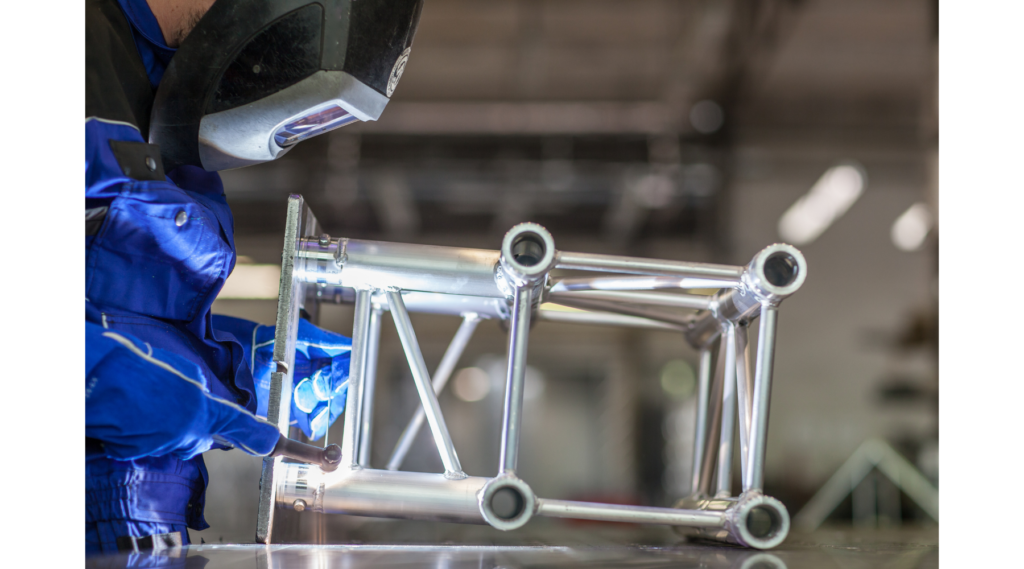
5. Lack of Quality Control Measures
Why It Matters: Quality control is essential for ensuring that fabricated parts meet specifications and function as intended. Neglecting quality control at any stage of the process can result in defective parts reaching the client, damaging the fabricator’s reputation.
Common Issues:
- Overlooking Tolerances: Parts fabricated outside tolerance limits may not assemble properly.
- Inconsistent Finishing: Poor surface finishing can affect the aesthetics and functionality of the part.
- Skipping Inspections: Neglecting inspection points throughout production can lead to unnoticed errors.
Example: A metal fabrication company produces custom brackets for an automotive client. Without proper quality control, some brackets were fabricated with holes slightly out of place. The error went undetected until final assembly, causing delays and requiring re-fabrication.
How to Avoid It:
- Implement rigorous quality checks at each stage of production, from initial design to final inspection.
- Use quality control tools, such as Coordinate Measuring Machines (CMM), to verify dimensions and tolerances.
- Establish a checklist for each step, including tolerance checks, finishing, and assembly fit.
Tip: ISO 9001 certification can improve quality control practices by setting consistent standards for production processes and inspections.
Conclusion
Metal fabrication is a precise and complex process, requiring careful planning, high-quality materials, and effective coordination. By avoiding these common mistakes—such as choosing unsuitable materials, making assumptions, mishandling storage, poor scheduling, and pursuing unrealistic designs—fabricators can optimize production and deliver top-quality results.
At LUX Metal, we understand the importance of precision and excellence in metal fabrication. Our expert team and state-of-the-art facilities allow us to tackle even the most challenging projects with confidence. To learn more about our metal fabrication services, visit our website at LUX Metal.
Further Reading
For more insights on metal fabrication, check out these resources: