Challenge of Decarbonizing Steelmaking
Steel production is energy-intensive, with traditional methods relying heavily on fossil fuels, particularly coal. In fact, steel manufacturing accounts for around 7-9% of global carbon dioxide emissions. This makes the steel industry one of the largest single industrial sources of greenhouse gas emissions. To address climate change, it is essential to drastically reduce carbon emissions throughout the steel value chain, from raw material extraction to end-product manufacturing.
The current carbon footprint of steel can be attributed to several factors:
- High Energy Consumption: Conventional steelmaking processes, such as the blast furnace-basic oxygen furnace (BF-BOF) method, require large amounts of energy, primarily derived from burning fossil fuels.
- Dependence on Coal: Coal is a major source of carbon emissions in steel production due to its use in smelting iron ore.
- Supply Chain Emissions: The transportation of raw materials, use of machinery, and logistics contribute significantly to the overall carbon footprint.
Decarbonization: The Key to a Sustainable Steel Industry
Decarbonizing the steel industry is no longer a choice but a necessity. The transition to a low-carbon economy involves reducing carbon emissions throughout the steel value chain, including raw material sourcing, production processes, and transportation. Governments, corporations, and industry stakeholders are collaborating to establish ambitious climate targets, which include reducing carbon emissions to net zero by 2050.
Strategies for Decarbonizing Steel Production
Decarbonization of the steel industry requires a multi-faceted approach. Below are some of the most promising strategies and technologies for reducing carbon emissions:
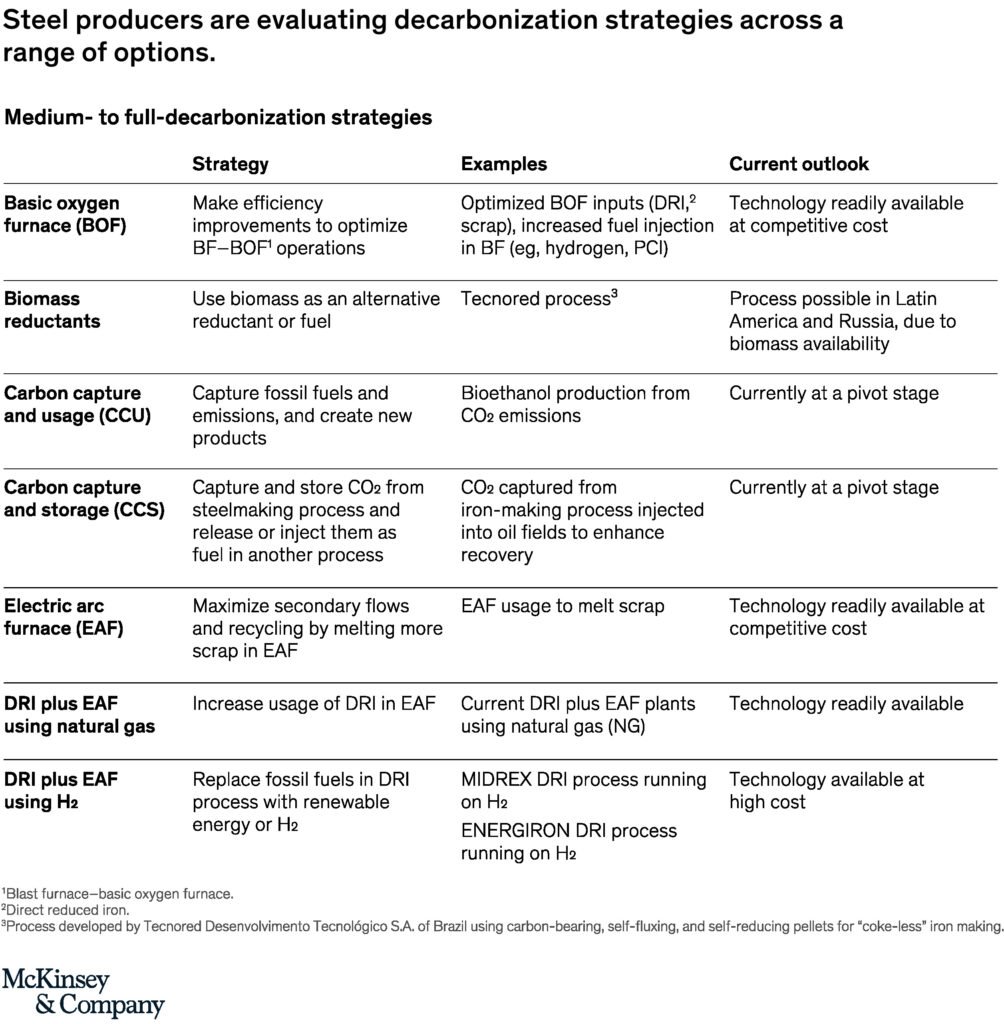
1. Green Hydrogen-Based Steelmaking
One of the most exciting innovations in decarbonizing steel production is the use of green hydrogen as a reducing agent. In traditional steelmaking, carbon from coal is used to reduce iron ore to iron. However, green hydrogen—produced using renewable energy sources like wind and solar—can replace carbon, significantly lowering emissions. When green hydrogen is used in steel production, the only byproduct is water, making it a cleaner alternative.
The benefits of hydrogen-based steelmaking include:
- Reduction of carbon emissions by up to 90%.
- Potential to replace conventional fossil fuel-based methods.
- Alignment with global climate targets for a low-carbon economy.
However, hydrogen-based steel production is currently more expensive than traditional methods due to high production costs and limited hydrogen availability. Advances in technology and increased production capacity are expected to drive down costs in the coming years.
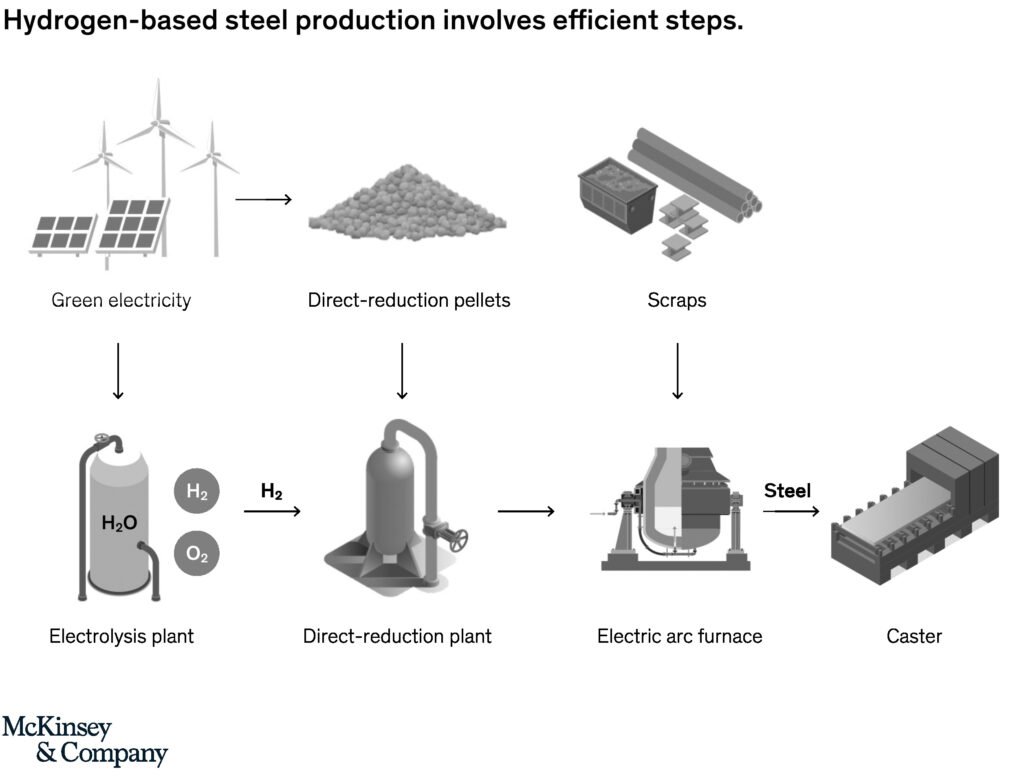
While CCS and CCU are both medium- and long-term economic options, hydrogen is a growing opportunity in the face of ambitious international climate targets. It is one of the few options for reducing emissions in steelmaking and could provide renewable developers a competitive advantage in the current paradigm. According to McKinsey’s SteelLens, hydrogen-based steel production could enable steel production that is nearly carbon-neutral
2. Electric Arc Furnaces (EAFs)
Electric Arc Furnaces (EAFs) are a more sustainable alternative to the traditional BF-BOF process. EAFs use electricity to melt scrap steel and iron, significantly reducing energy consumption and carbon emissions. If the electricity used is sourced from renewable energy, the process can be almost carbon-neutral.
The advantages of EAFs include:
- Lower carbon emissions compared to conventional steelmaking.
- Increased use of recycled scrap steel, promoting circular economy principles.
- Flexibility to be powered by renewable energy sources.
While EAFs are a promising solution, they require a consistent supply of high-quality scrap steel. This challenge is being addressed through improved scrap collection and recycling infrastructure.
3. Carbon Capture, Utilization, and Storage (CCUS)
Carbon Capture, Utilization, and Storage (CCUS) technology involves capturing carbon emissions generated during steel production and either storing them underground or using them for other industrial processes. CCUS can reduce carbon emissions from existing steel plants, making it a viable solution for retrofitting older facilities.
Key benefits of CCUS include:
- Compatibility with existing steel production infrastructure.
- Potential to capture and reuse carbon emissions for valuable products, such as chemicals and fuels.
- Contribution to a circular economy by reducing the environmental impact of steel production.
Despite its potential, CCUS technology is still in the early stages and faces challenges related to scalability, cost, and infrastructure development.
4. Use of Low-Carbon Raw Materials
The choice of raw materials can significantly impact the carbon footprint of steel production. Utilizing low-carbon raw materials, such as iron ore pellets and direct reduced iron (DRI), can reduce the energy requirements and emissions associated with steelmaking. Additionally, increasing the proportion of recycled steel in the production process further contributes to sustainability.
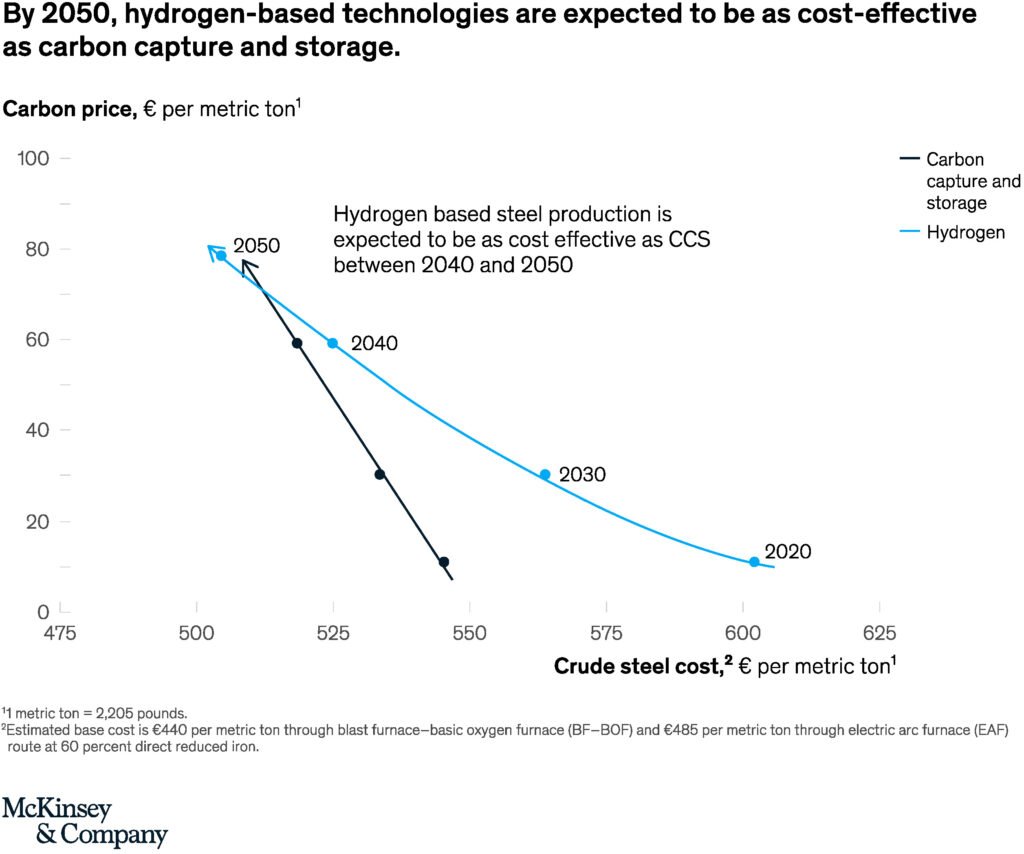
Adopting CCS or CCU technology in existing blast furnaces would add operational expenditure of approximately €100 per ton of crude steel, and hydrogen-based steel production would cost approximately €170 per ton of crude steel. By 2050, with increases in scaled hydrogen production and carbon taxes, hydrogen-based steel production, CCS, and CCU will provide competitive options for steelmakers
The Role of Circular Economy in Steel Decarbonization
The concept of a circular economy is integral to decarbonizing the steel industry. A circular economy focuses on minimizing waste and maximizing resource efficiency through recycling, reuse, and sustainable practices. For the steel industry, this means:
- Increased Recycling: Boosting the use of scrap steel reduces the need for virgin raw materials and lowers carbon emissions.
- Waste Reduction: Implementing waste management strategies to minimize waste generation throughout the steel value chain.
- Product Longevity: Designing steel products for longer lifespans, reducing the frequency of replacements and conserving resources.
Renewable Energy Integration in Steel Manufacturing
Decarbonizing the steel industry goes hand in hand with increasing the use of renewable energy sources. Steel manufacturers are increasingly integrating renewable energy, such as solar and wind, into their operations to power machinery, reduce reliance on fossil fuels, and decrease carbon emissions. Companies that transition to green energy not only lower their carbon footprint but also future-proof their operations against potential carbon taxes and regulatory changes.
The Future of Green Steel and Lux Metal’s Commitment
The future of the steel industry lies in its ability to embrace green steel solutions and sustainable practices. Green steel—produced using low-carbon technologies—represents a paradigm shift in the industry, offering a cleaner, more efficient way to produce steel without sacrificing quality.
At Lux Metal, we are committed to being part of the solution. As a leading steel manufacturer, we understand the importance of sustainability and are actively pursuing initiatives to reduce our carbon footprint. Our state-of-the-art facilities are equipped with advanced machinery that promotes efficiency, waste reduction, and the use of recycled materials. We are continuously exploring opportunities to adopt greener technologies, such as hydrogen-based steelmaking and renewable energy integration, to stay ahead of industry trends and support global climate goals.
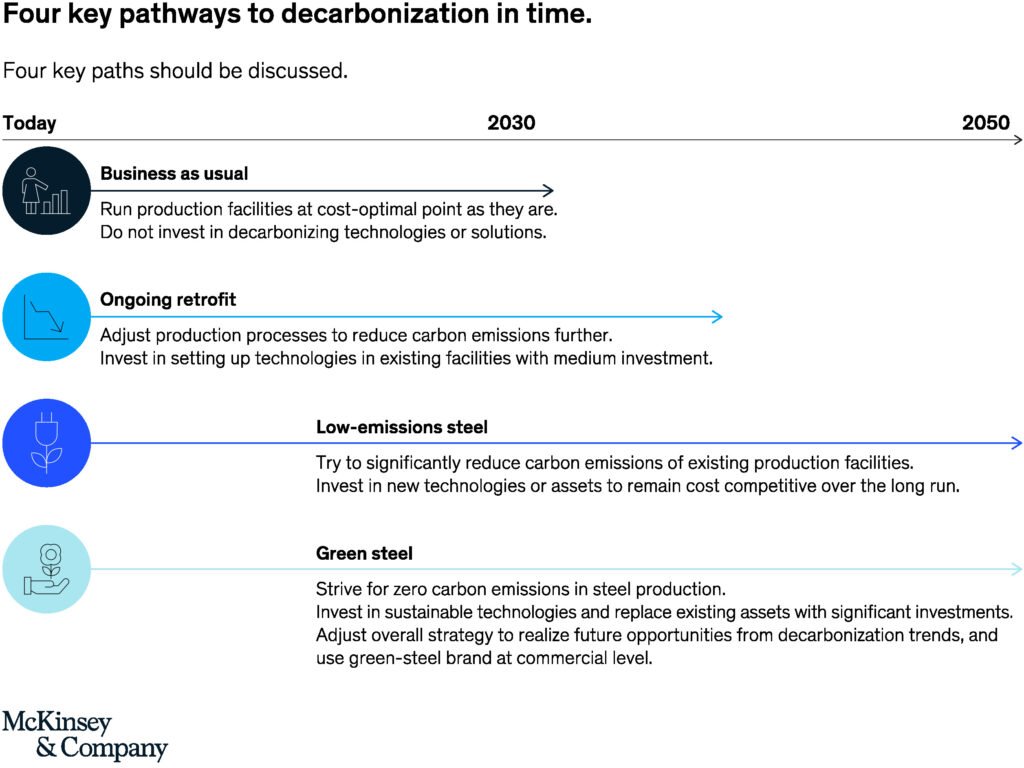
Lux Metal’s Sustainable Solutions for a Better Future
Our dedication to sustainability goes beyond our production processes. We strive to provide our customers with steel solutions that align with eco-friendly practices. By choosing Lux Metal, you are not only investing in high-quality steel products but also supporting a greener and more sustainable steel industry. Our range of products is designed to meet diverse needs, from construction and manufacturing to agricultural applications, while adhering to the highest environmental standards.
Explore our range of eco-friendly products at Lux Metal and join us in the journey toward a decarbonized steel industry. Contact us today for more information, or visit our website at www.luxmetalgroup.com.
References:
Decarbonizing the Steel Value Chain
Tackling the Challenge of Decarbonizing Steelmaking
Decarbonization Challenge for Steel