1. The Role of Design in Laser Cutting
The metal laser cutting process begins long before a laser touches the material. The first step is creating a precise design. Engineers and designers use advanced software tools like CAD (Computer-Aided Design) to draft detailed blueprints of the desired components.
Key considerations during the design phase include:
- Material Selection: The type of metal (e.g., stainless steel, aluminum, or titanium) influences cutting parameters like laser power and speed.
- Thickness: The material’s thickness determines the optimal laser settings and cutting techniques.
- Complexity of the Design: Intricate patterns and tight tolerances require meticulous planning and high-quality CAD models.
Once the design is finalized, the file is converted into a format compatible with the laser cutting machine, such as DXF or DWG. These files guide the laser cutter’s movements with precision.
2. The Science Behind Laser Cutting
At its core, laser cutting uses a concentrated beam of light to slice through metal. This process involves several key components:
- Laser Source: High-powered lasers, such as CO2, fiber, or diode lasers, generate the light beam.
- Beam Delivery System: Mirrors and lenses focus and direct the laser beam to the cutting head.
- Assist Gas: Gases like nitrogen, oxygen, or argon are used to enhance cutting efficiency and prevent oxidation.
The laser beam’s energy heats the metal to its melting or vaporization point. Simultaneously, the assist gas blows away molten material, leaving a clean, precise cut.
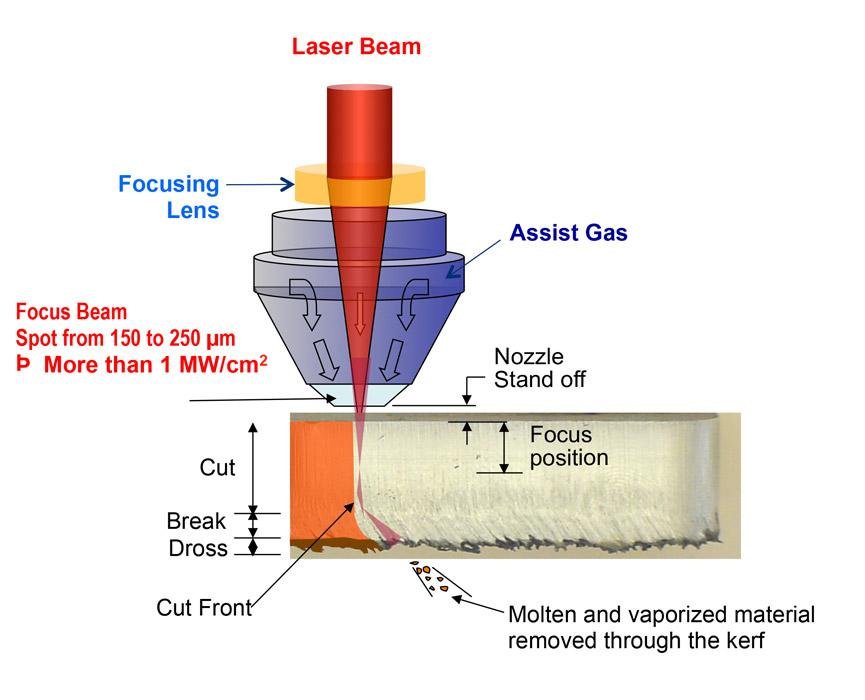
Reference: Laser cutting basics: The science of burr-free laser cutting
3. Types of Laser Cutting Techniques
The choice of cutting technique depends on the material and desired outcome. The most common methods include:
- Fusion Cutting: The laser melts the metal, and an inert gas expels the molten material. This technique is ideal for stainless steel and aluminum.
- Flame Cutting: Oxygen reacts with the heated metal, creating an exothermic reaction that facilitates cutting. This is commonly used for carbon steel.
- Vaporization Cutting: The laser rapidly heats the metal, causing it to vaporize. This method is used for thin materials and intricate designs.
Each technique has its advantages and applications, making laser cutting versatile for various industries.
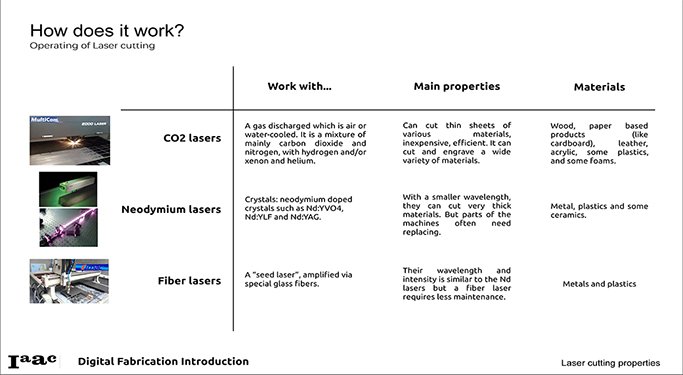
Reference: Laser cutting properties
4. The Laser Cutting Process in Action
Once the design is uploaded and the machine settings are calibrated, the cutting process begins. Here’s a step-by-step breakdown:
- Material Placement: The metal sheet is secured on the machine’s cutting bed to ensure stability.
- Calibration: The laser cutter adjusts its focus and settings based on the material and design specifications.
- Cutting: The laser follows the programmed path, cutting the material with remarkable precision.
- Quality Check: After cutting, components are inspected for accuracy, edge quality, and adherence to design specifications.
5. Advantages of Metal Laser Cutting
Metal laser cutting offers numerous benefits over traditional cutting methods:
- Precision: Lasers can achieve tolerances as tight as 0.001 inches, ensuring exact cuts.
- Speed: The process is significantly faster than mechanical cutting, reducing production time.
- Versatility: From intricate patterns to thick metal sheets, lasers handle diverse cutting requirements.
- Minimal Waste: Laser cutting optimizes material usage, reducing waste and saving costs.
- Clean Edges: The cuts are smooth and burr-free, eliminating the need for additional finishing.
6. Applications Across Industries
The versatility of metal laser cutting makes it a critical tool in various industries:
- Automotive: Creating intricate components like gears and panels.
- Aerospace: Fabricating lightweight yet strong parts for aircraft.
- Architecture: Designing decorative metal panels and structural components.
- Electronics: Precision cutting of tiny components for circuits and devices.
- Medical Devices: Manufacturing surgical instruments and implants with exact dimensions.
7. Challenges and Solutions in Laser Cutting
Despite its advantages, laser cutting has challenges, including:
- Material Limitations: Some reflective metals, like copper and brass, require specialized lasers.
- Heat Affects: Improper settings can cause warping or discoloration.
- Cost: High initial investment in laser cutting equipment.
Solutions include using advanced lasers, regular maintenance, and skilled operators to optimize performance.
8. The Future of Metal Laser Cutting
As technology evolves, metal laser cutting continues to advance:
- Automation: Integration with robotics for fully automated cutting systems.
- AI and Machine Learning: Predictive algorithms to enhance precision and efficiency.
- Green Technologies: Development of eco-friendly lasers and energy-efficient systems.
These innovations promise to make laser cutting even more accessible and sustainable.
Conclusion
Metal laser cutting represents the pinnacle of precision manufacturing. From the meticulous design phase to the final product, every step of the process reflects a commitment to accuracy, efficiency, and innovation. As industries demand higher standards and faster production, laser cutting remains at the forefront, shaping the future of manufacturing. Whether you’re an engineer, designer, or business owner, understanding this process unlocks new possibilities for creating superior products.
By mastering the science and art of metal laser cutting, you can achieve unparalleled results—from design to precision.
Partner with Lux Metal for Premium Steel Solutions
For businesses seeking high-quality steel products and customized metal solutions, Lux Metal is your trusted partner. Visit our website to explore our wide range of services and see how we can help you meet your industrial needs with precision and excellence.